Liquid Silicone Injection Molding Process for Waterproof Encapsulation and Silicone to Metal Overmolding of Mobile Phone Card Trays
Item specifics
- Product name
- Waterproof mobile phone card tray
- Waterproof grade
- IP68
- Product Material
- Silicone to Metal Overmolding
- Applications
- Electronic waterproof
- Product process
- One-piece molding
- Processing accuracy
- 0.003mm
- Product size control accuracy
- +-0.03mm
Review
Description
Product Advantages
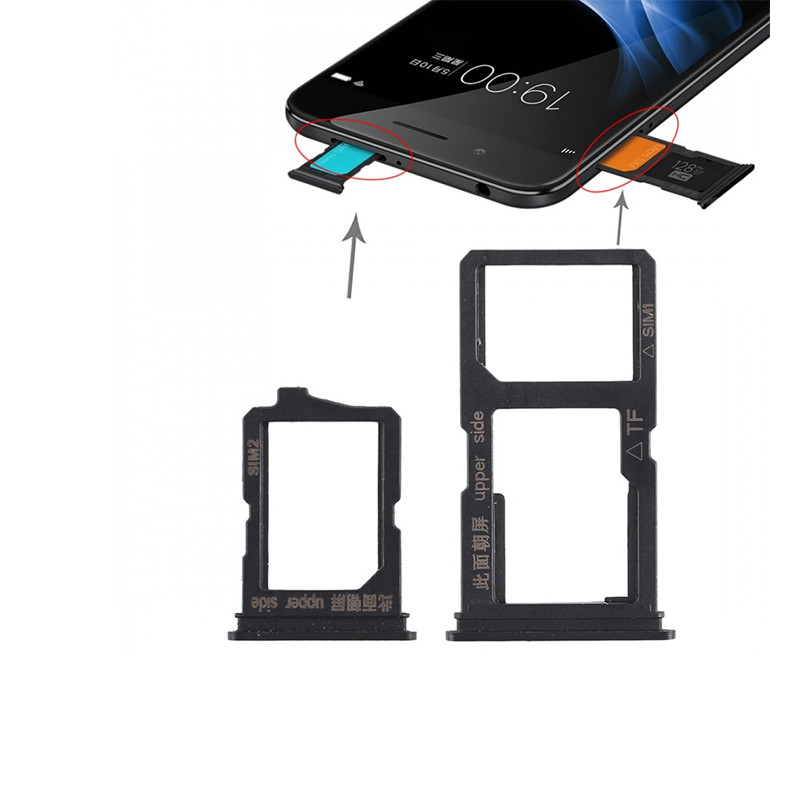
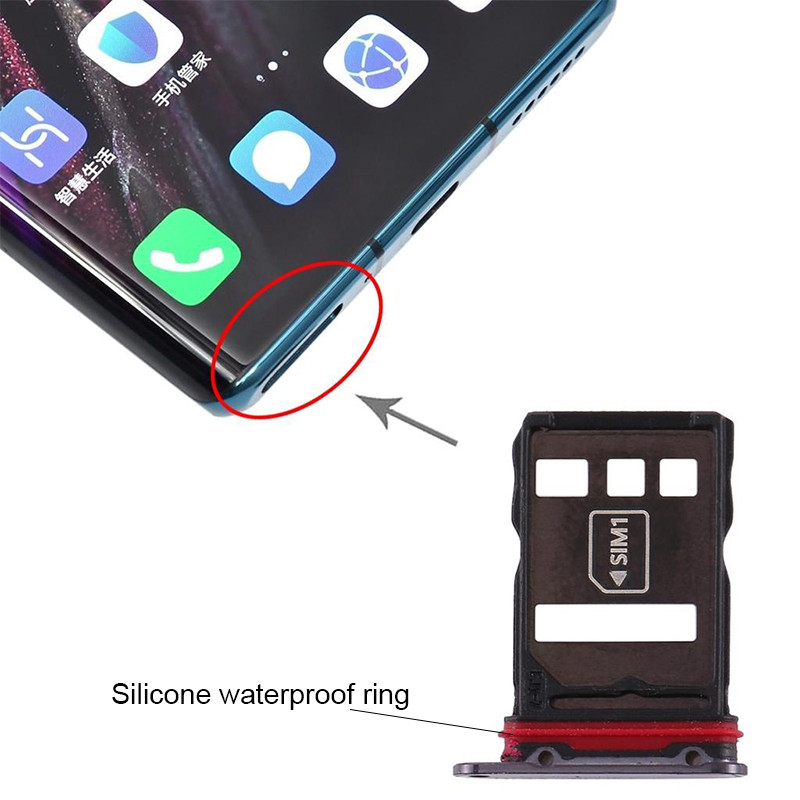
For hardware mobile phone card tray waterproof encapsulation products, customers in the market usually face the following pain points. As a professional 3C electronic mobile phone silicone encapsulation and Silicone to Metal Overmolding source factory, Siliconeplus has its own mold room and independent mold production capabilities, which can effectively solve these pain points:
1. Unstable waterproof effect
Pain point: The waterproof encapsulation effect of the card tray is not ideal, resulting in the inability to effectively protect the inside of the SIM card tray when the mobile phone is exposed to water, which in turn affects the overall waterproof performance of the mobile phone.
Solution: Siliconeplus uses high-precision liquid silicone encapsulation technology to ensure that the waterproof sealing of each card tray interface meets the IP67 or IP68 standard, and through strict testing, ensures the stable protection effect of the product in a water environment.
2. Insufficient adhesion between silicone and metal card tray
Pain point: In the card tray encapsulation product, the adhesion between silicone and the metal substrate is not strong enough, resulting in the easy fall-off of the encapsulated part, affecting the waterproof effect.
Solution: Siliconeplus uses professional surface treatment and silicone bonding technology to ensure that the silicone adheres firmly to the metal card tray, effectively preventing degumming and enhancing the overall durability and protection of the card tray.
3. Dimensional accuracy and batch consistency issues
Pain point: Customers require high-precision card tray products to ensure precise matching with the mobile phone card slot. However, many suppliers have difficulty in ensuring dimensional consistency in mass production, which may cause the product to jam or fail to install during assembly.
Solution: Siliconeplus uses its own mold room and precision mold design, combined with advanced injection molding technology, to ensure the dimensional accuracy and batch consistency of the card tray encapsulated products, avoiding the impact of dimensional deviation on assembly and use.
4. Surface defects caused by demolding difficulties
Pain point: The card tray is prone to sticking during the demolding process, resulting in surface defects or damage, affecting the appearance and performance of the product.
Solution: Siliconeplus uses optimized mold design and advanced demolding technology to ensure that the card tray can be demolded smoothly, keep the product surface smooth, and ensure high-quality appearance and consistency.
5. Waterproof encapsulation affects the ease of use of the card tray
Pain point: Too thick or uneven waterproof encapsulation may make it difficult to insert and remove the card tray in the mobile phone, affecting the user experience.
Solution: Siliconeplus uses precision injection molding to ensure that the thickness of the encapsulation layer is uniform and moderate, so that the card tray can be easily inserted and removed, taking into account both waterproof performance and user convenience.
6. Improper material selection affects durability
Pain point: Some card tray encapsulation products on the market use inferior materials, which causes aging or cracking in high temperature, low temperature or humid environment, affecting the service life.
Solution: Siliconeplus uses high-quality liquid silicone materials with excellent high temperature resistance, low temperature resistance and anti-aging properties to ensure that the product maintains good performance and durability under different environmental conditions.
7. Waterproof encapsulation affects the conductivity of metal
Pain point: The metal part of the card tray usually needs to have a certain conductivity. If the encapsulation is not handled properly, the conductivity may be affected.
Solution: Siliconeplus uses precise encapsulation technology to ensure that the metal parts are effectively protected during the encapsulation process, ensuring that the metal part of the card tray still has good conductivity after waterproofing.
8. Unstable delivery cycle
Pain point: Customers have high requirements for delivery cycle, especially in the fierce competition in the mobile phone accessories market, and fast delivery is crucial to maintaining market competitiveness. Many suppliers find it difficult to ensure stable delivery time.
Solution: Siliconeplus shortens the time from design to production through its own mold room and integrated production capacity, and can complete mass production within 3-4 weeks, ensuring timely delivery, helping customers seize the initiative in the fiercely competitive market.
With its professional technology and production experience, Siliconeplus can effectively solve the pain points encountered by customers in the waterproof encapsulation of hardware mobile phone card trays, provide high-quality and reliable products, and help customers improve their market competitiveness.
Product advantages and features
High durability: The card tray after liquid silicone encapsulation has extremely high wear resistance, tear resistance and long service life, is not easy to deform or damage, and can cope with various wear and tear in daily use.
Good sealing: Silicone material has good elasticity and sealing, can tightly wrap the card tray, ensure seamless connection, prevent foreign substances from penetrating, and improve the overall reliability of the product.
High and low temperature resistance: Silicone can maintain stable performance at extreme temperatures and is suitable for various harsh environments. Whether it is high or low temperature, it can ensure the normal operation of the card tray.
Environmentally friendly material: Liquid silicone is a non-toxic and harmless environmentally friendly material that meets international environmental standards, is safe to use, and is harmless to the human body. It is suitable for the sealing and protection of electronic products.
Excellent flexibility: Silicone material has excellent flexibility, which protects the card tray without affecting its installation and removal, ensuring convenient use.
Strong corrosion resistance: The silicone-coated card holder can effectively prevent corrosion from various chemicals, further improving the service life and durability of the product.
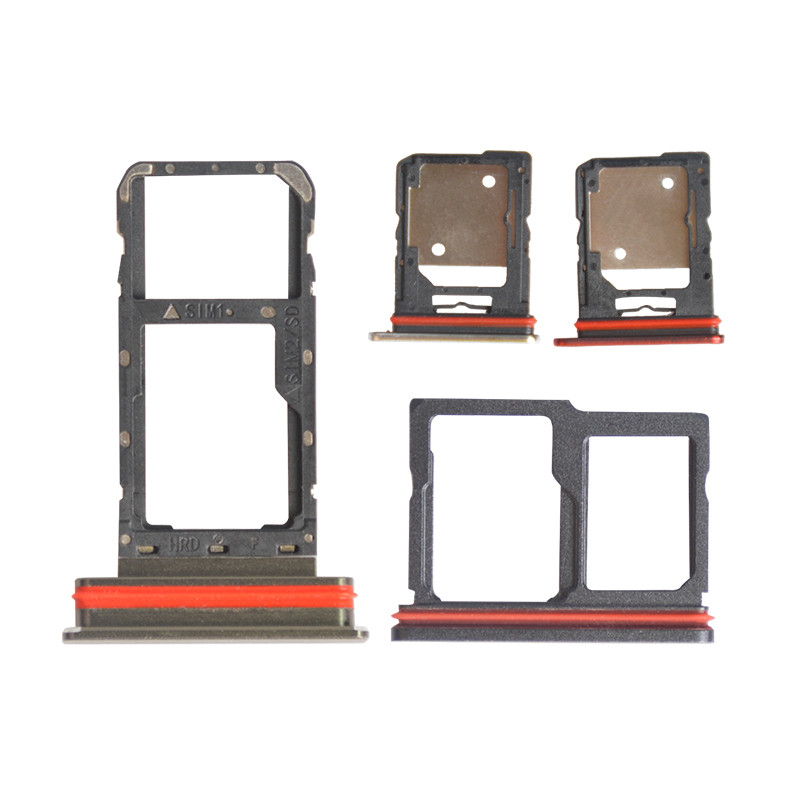
Customization process
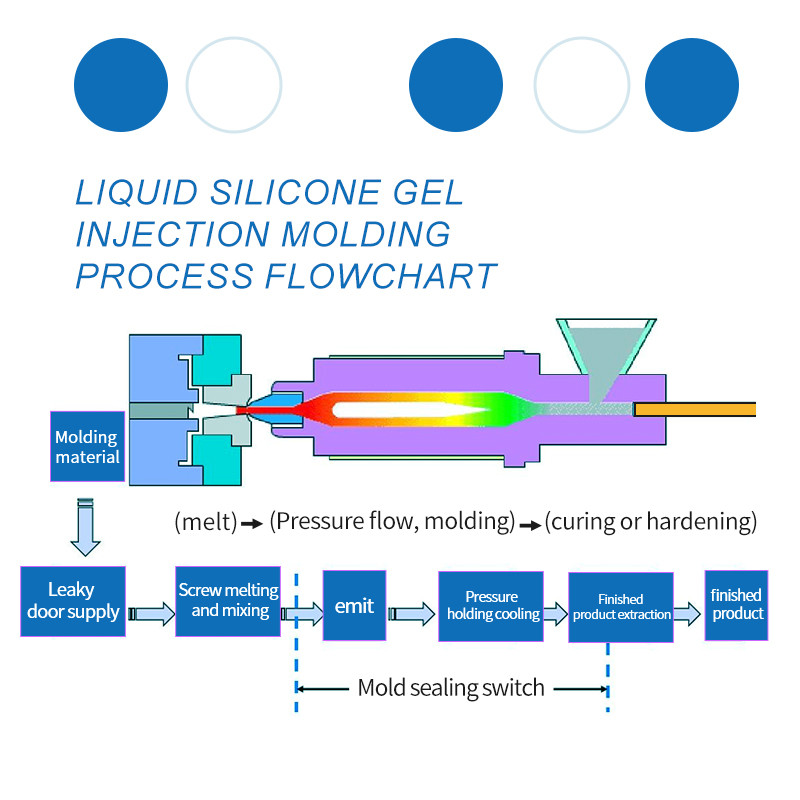
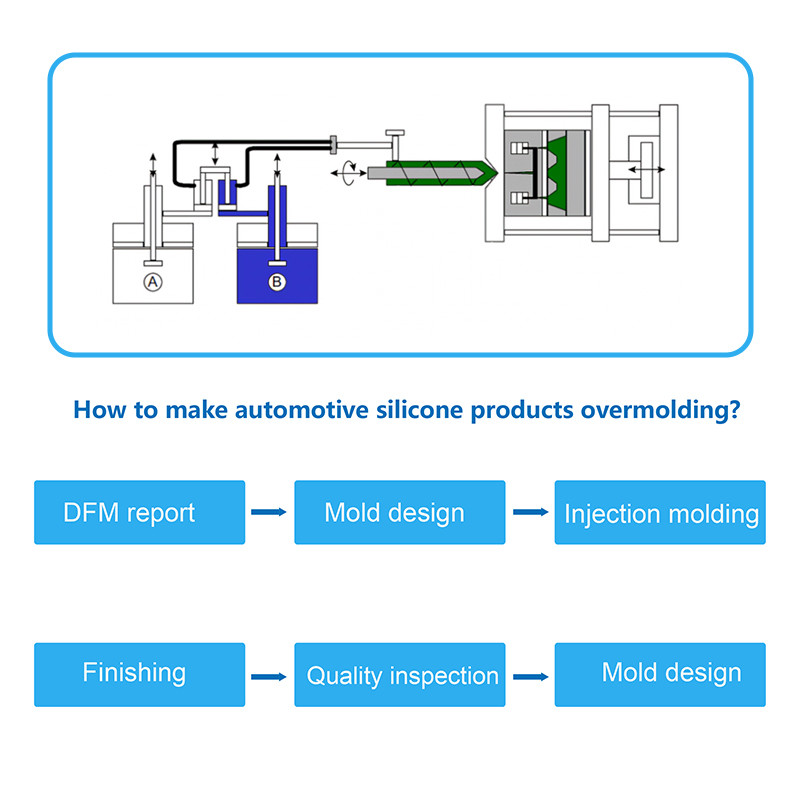
Customer Cases
A world-renowned mobile phone brand (hereinafter referred to as the "client") encountered difficulties in the waterproof performance and production consistency of hardware mobile phone card trays when developing a new smartphone. As the market has put forward higher requirements for the waterproof function of smartphones, this new phone needs to reach the IP68 waterproof level, but the card tray encapsulation products provided by the existing supplier have unstable quality in mass production and are difficult to meet the underwater sealing requirements of mobile phones. In addition, the client also requires mass production to be completed in a short time in order to prepare stocks before the new product is released.
Challenges faced
Insufficient waterproof performance: The original supplier's card tray waterproof encapsulation products are difficult to meet the IP68 grade requirements, and water leaks in underwater pressure environments, affecting the waterproof performance of the entire device.
Dimensional accuracy and consistency issues: In mass production, there is a large deviation in the dimensional accuracy of the card tray, which causes some products to get stuck or unable to be inserted into the card slot during assembly.
Insufficient bonding: The bonding strength between the silicone and the metal card tray is insufficient, and the card tray is prone to debonding during use, affecting the overall protection effect and appearance of the mobile phone.
Siliconeplus Solution Customers found Siliconeplus, hoping to solve these problems through our professional technology and production experience. As a professional 3C electronic silicone encapsulation processing source factory, Siliconeplus helped customers overcome challenges through the following solutions:
Precision encapsulation process to ensure waterproof performance
We use liquid silicone injection molding technology and perform special surface treatment on the metal card tray to ensure that the silicone and metal are tightly combined. After a series of rigorous waterproof tests, the final product can stably meet the IP68 waterproof standard to ensure the normal use of the mobile phone underwater.
Own mold room, improve dimensional accuracy and consistency
Siliconeplus has its own mold room and professional mold design team to customize precision molds for customers' card tray products, and through high-standard production process control, ensure dimensional consistency in mass production. In the end, each card tray can perfectly fit the mobile phone card slot, and there will be no more problems of jamming and inability to insert.
Improve adhesion and ensure product durability
Through professional surface pretreatment and bonding process, we have greatly improved the bonding strength between silicone and metal, ensuring that the product will not debond during long-term use, and at the same time improving the stability of the card tray in extreme environments.
FAQs about Customized Mobile Phone Card Tray Waterproof Encapsulation
Can the product's waterproof performance meet the IP67 or IP68 standards? Can it be used underwater for a long time to prevent water from entering the SIM card slot?
Siliconeplus uses a high-precision encapsulation process to ensure that the product's waterproof level meets the IP67 or IP68 standards, which can effectively prevent water from entering the SIM card slot and protect the internal electronic components of the mobile phone.
Is the bond between the silicone and the metal tray strong? Will there be problems such as debonding and cracking during use?
We use professional bonding technology and surface treatment technology to ensure that the silicone and metal tray are firmly bonded, and can remain stable even during frequent plugging and unplugging to prevent debonding.
During the production process, how to ensure that the tray can be demoulded smoothly and avoid surface damage or defects?
Siliconeplus uses optimized mold design and demoulding technology to ensure that the product can be demoulded smoothly, the surface is not damaged, the appearance is smooth, and it meets high quality standards.