best way to deflash silicone overmold?
- Share
- publisher
- siliconeplus editor
- Issue Time
- Sep 5,2024
Summary
The best way to deflash silicone overmold products depends on the type of product, mold design, and production scale. Here are some of the most effective methods:
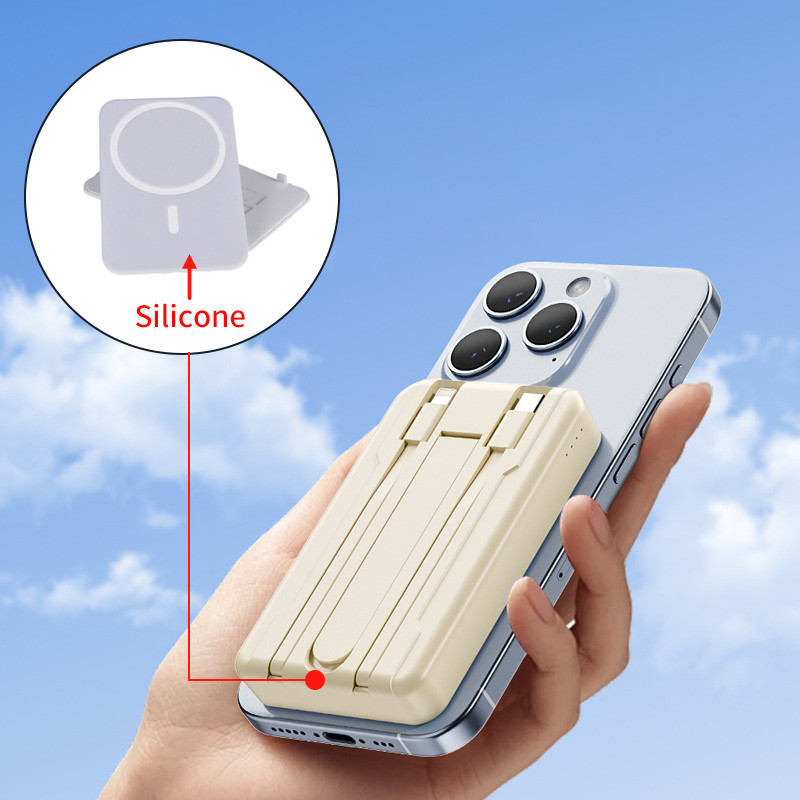
best way to deflash silicone overmold?
The best way to deflash silicone overmold products depends on the type of product, mold design, and production scale. Here are some of the most effective methods:
Manual Deflashing:
Suitable for smaller production runs or complex shapes.
Workers use precision cutting tools, scissors, or blades to remove excess silicone material manually.
Ideal for delicate or intricate parts, but can be time-consuming.
Cryogenic Deflashing:
Involves freezing the parts using liquid nitrogen, which makes the silicone flash brittle.
Once brittle, a tumbling process or blasting with small pellets removes the flash without damaging the product.
This is a fast, automated solution for large production runs.
Laser Deflashing:
Uses a laser to vaporize excess silicone flash.
It's highly precise and efficient, especially for high-tech industries where precision is crucial.
Suitable for complex and sensitive components but can be costly due to advanced equipment.
Tumbling:
Involves placing the silicone parts in a tumbling machine with abrasive media to remove flash.
This method works well for simpler parts but may not be suitable for parts with delicate or intricate features.
Chemical Deflashing:
Uses specific solvents that dissolve excess flash without affecting the silicone overmold itself.
This method is less common due to the environmental impact and the need for careful chemical selection.
Trimming with CNC Machining:
For precise and controlled deflashing, CNC machines can be used to trim off excess material.
This method provides excellent results for parts that need high precision.
Choosing the Best Method:
The most appropriate deflashing technique depends on factors like the size and complexity of the parts, the volume of production, and the desired finish quality. For high-volume runs, cryogenic or laser deflashing is often preferred for speed and precision, while manual deflashing remains ideal for custom or low-volume production.