What is medical silicone injection molding?
- Share
- publisher
- Siliconeplus Editor
- Issue Time
- May 15,2025
Summary
Medical silicone injection molding is a process that uses liquid silicone rubber (LSR) and specialized molding techniques to produce high-precision, biocompatible medical parts.
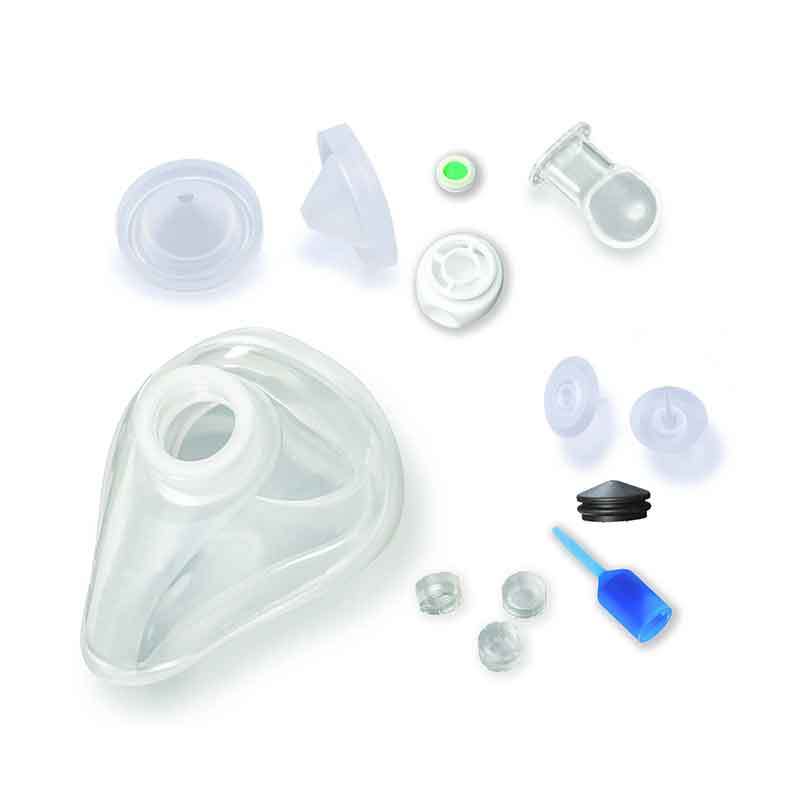
When designing medical parts, precision and safety come first. But not all materials and processes can meet the challenge.
Medical silicone injection molding is a process that uses liquid silicone rubber (LSR) and specialized molding techniques to produce high-precision, biocompatible medical parts.
I once worked on a project for a medical client who needed thousands of soft, skin-safe parts for a wearable device. That’s when I truly saw how powerful this technology is.
[Table of contents]
Why is silicone used in medical injection molding?
What are the benefits of using medical-grade silicone?
How does the injection molding process work for medical parts?
What are the key applications in the medical field?
Why is silicone used in medical injection molding?
Silicone is not the only material, but it solves many unique problems in medical device manufacturing.
Silicone is flexible, durable, biocompatible, and can withstand sterilization—making it ideal for medical injection molding.
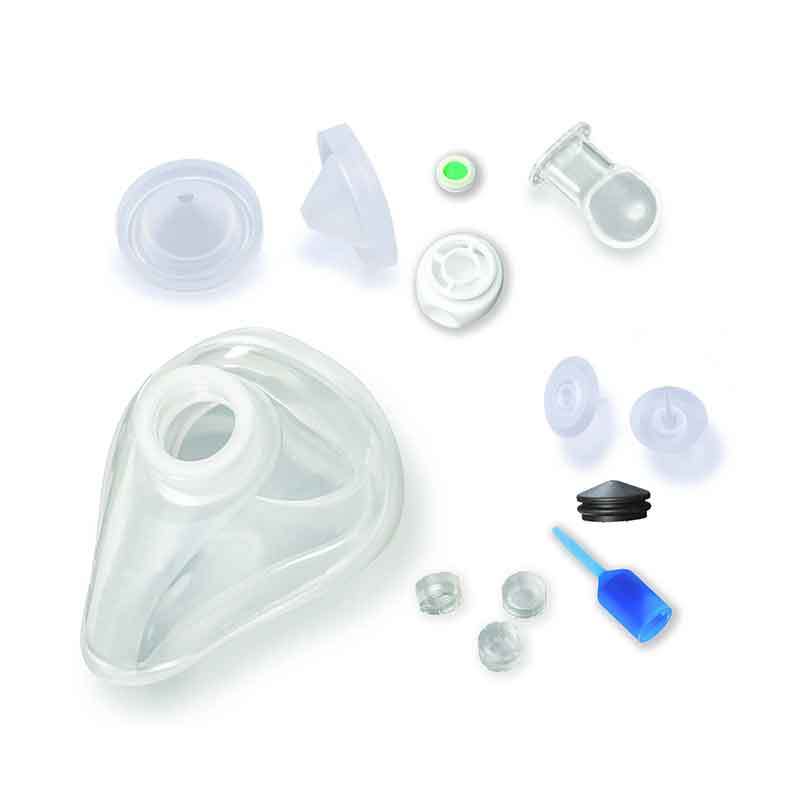
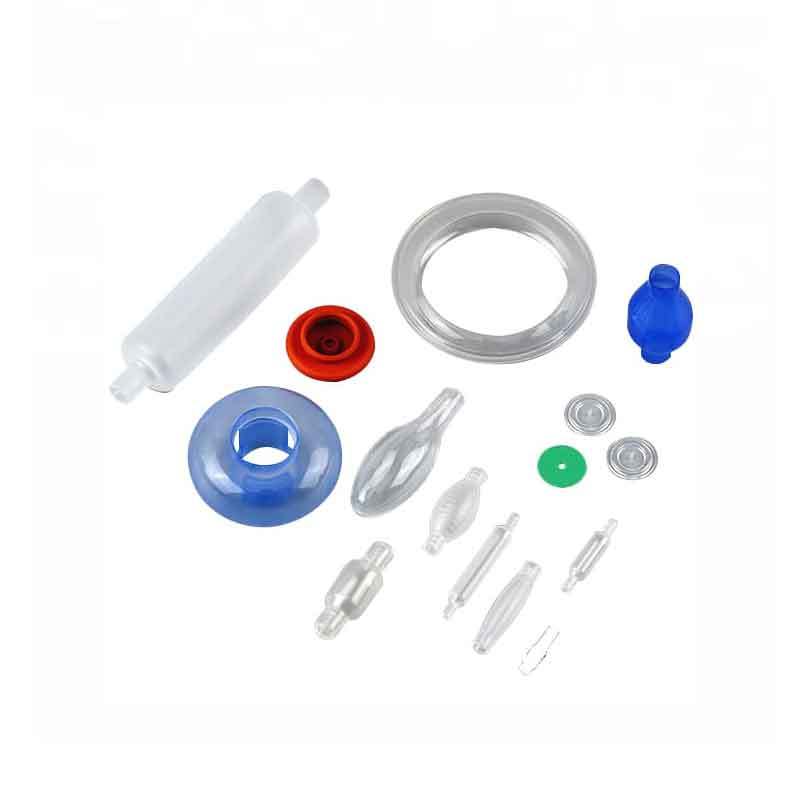
Dive Deeper: What makes silicone stand out?
Medical devices often require materials that:
Can bend and flex without tearing
Are non-reactive with skin or tissue
Handle high-temperature sterilization (like autoclaving)
Silicone checks all the boxes. Unlike thermoplastics, it resists degradation and doesn’t leach chemicals. In operating rooms or inside the body, that matters.
Here’s a quick comparison:
Property | Silicone | Thermoplastics |
Biocompatibility | Excellent | Varies |
Heat Resistance | Up to 200°C | Usually <120°C |
Flexibility | Very high | Depends on material |
Sterilization-ready | Yes (Autoclave, ETO) | Sometimes |
What are the benefits of using medical-grade silicone?
Clients often ask me why we don't use cheaper materials. The answer is simple: safety and reliability.
Medical-grade silicone is non-toxic, resistant to microbes, and approved for human contact by regulatory bodies.
Dive Deeper: Why certification and purity matter?
When producing for the medical field, compliance isn’t optional. Certified LSR materials:
Are tested for cytotoxicity
Meet USP Class VI or ISO 10993 standards
Have traceability and batch control
These properties give medical engineers peace of mind. Patients' lives depend on these parts performing under strict conditions, often inside the human body.
How does the injection molding process work for medical parts?
Some people think injection molding is just for plastic toys. The medical version is far more refined.
Medical silicone injection molding uses liquid silicone rubber (LSR), which is injected into heated molds under precise conditions.
Dive Deeper: The key steps of the process
Material Prep: Two-part LSR is stored in separate drums and mixed right before molding.
Injection: The material is injected into the mold cavity at controlled pressure.
Curing: Heat initiates a fast cross-linking reaction.
Demolding: Once cured, parts are ejected automatically or manually.
Post-processing: Some products may require deflashing, inspection, or secondary bonding.
This method creates flash-free, high-tolerance components. It also allows for overmolding with metal or plastic parts.
What are the key applications in the medical field?
When I show samples to clients, they’re often surprised at the variety of products we can make.
Medical silicone injection molding is used in tubing, seals, masks, catheters, and implantable parts.
Dive Deeper: Application breakdown by function
Respiratory & Anesthesia
Oxygen masks
Seals for CPAP machines
Surgical & Implantable
Soft tissue implants
Valve parts
Diagnostic & Wearables
Biosensor enclosures
Skin-contact electrodes
Silicone’s softness, stability, and custom color options also make it ideal for consumer health and wellness products.
Conclusion
Medical silicone injection molding delivers precision, safety, and reliability.