Unlocking the Power of Silicone: Applications, Techniques, and Advantages Across Industries
- Share
- publisher
- Siliconeplus Editor
- Issue Time
- Nov 7,2024
Summary
To meet industry demands for high-quality silicone products, Siliconeplus employs advanced silicone manufacturing techniques that enhance product quality and performance.
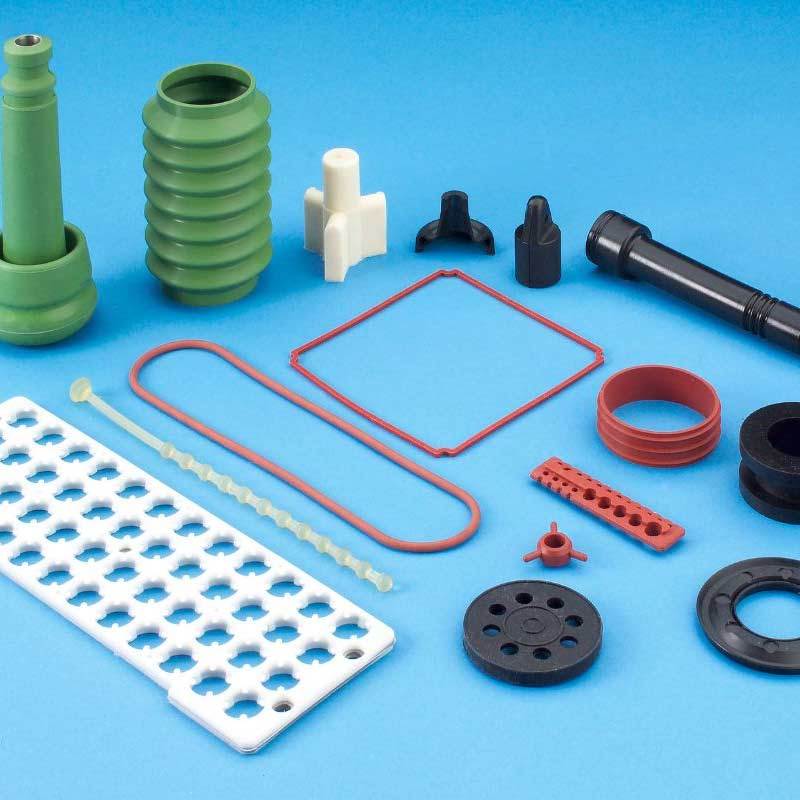
Silicone products, especially custom solutions like those offered by Siliconeplus, have become essential across diverse industries. Known for their flexibility, durability, and high-performance characteristics, silicone products offer exceptional value. In this post, we’ll explore the various applications of silicone, the technical processes involved, and the unique benefits silicone brings to different sectors. Key terms such as custom silicone solutions, silicone applications, high-performance silicone, and silicone manufacturing techniques will guide our journey.
Silicone Applications Across Industries: Adding Value with Custom Solutions
Silicone has been a transformative material across many fields due to its versatility and adaptability. Siliconeplus specializes in creating custom silicone solutions that meet specific industry requirements, combining silicone with materials like metal, plastic, and flexible printed circuits (FPC). Below are some industries where silicone has proven invaluable:
Medical Devices
Silicone is widely used in the medical field because of its biocompatibility and resistance to bacteria. Applications include medical tubing, implants, and custom silicone medical masks that conform to patients’ needs. At Siliconeplus, we ensure that our silicone meets strict medical standards, providing reliable, durable solutions that enhance patient safety.
Automotive and Aerospace
For industries demanding materials that withstand extreme temperatures and high-stress environments, silicone offers excellent temperature resistance and vibration dampening properties. From gaskets to sealants and thermal insulation components, silicone provides durability and performance. Siliconeplus utilizes advanced compression molding techniques to create high-performance automotive and aerospace parts that resist aging and ensure longevity.
Electronics
In electronics, silicone encapsulation and waterproofing solutions protect components from moisture and environmental factors, essential in wearable and outdoor devices. By integrating silicone with FPCs, Siliconeplus provides silicone encapsulation solutions that enhance electronic components' durability and reliability.
Industrial and Consumer Goods
Silicone’s flexibility and non-toxic nature make it ideal for consumer products, from kitchenware to baby toys. In industrial applications, silicone plays a role in sealing, insulation, and waterproofing. Siliconeplus can produce custom silicone parts that align with specific requirements, supporting clients in creating safer and more reliable products.
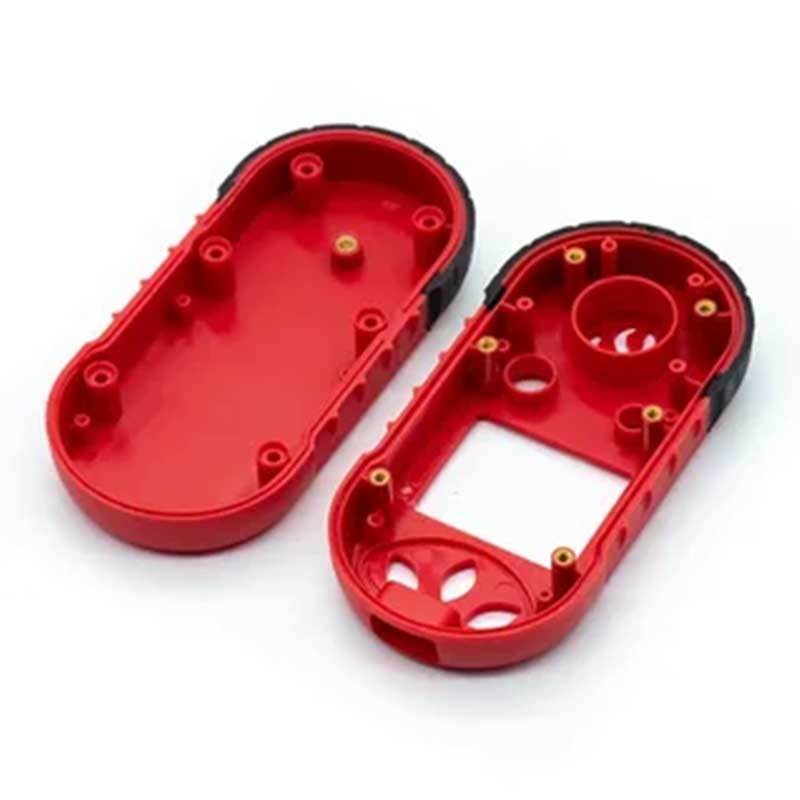
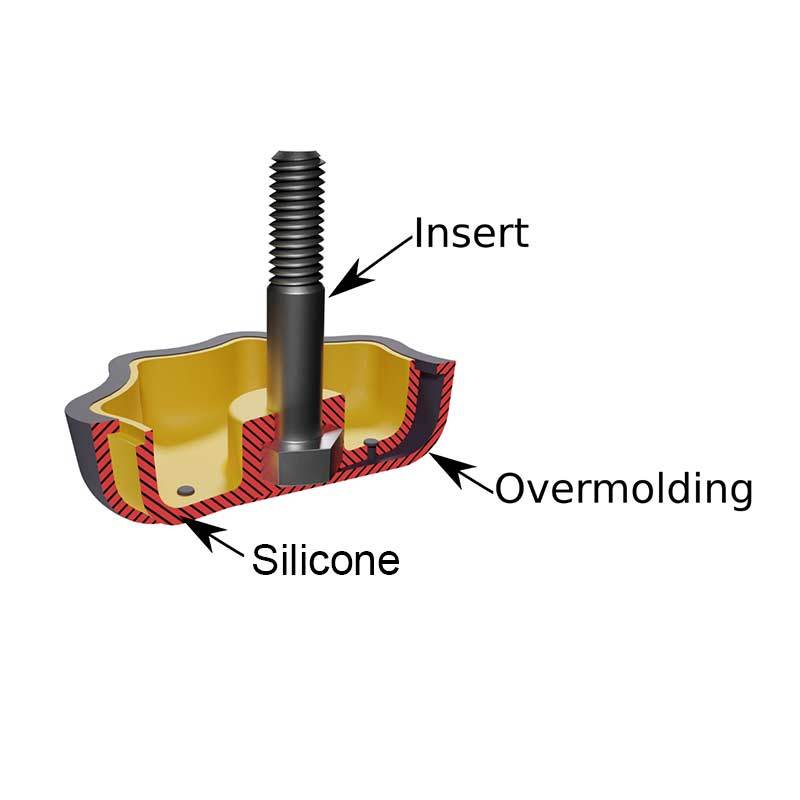
Silicone Manufacturing Techniques: How Siliconeplus Creates Quality Products
To meet industry demands for high-quality silicone products, Siliconeplus employs advanced silicone manufacturing techniques that enhance product quality and performance.
Compression Molding Process
The compression molding process involves placing uncured silicone rubber in a heated mold, where it is shaped under high pressure to produce precise parts. This method is ideal for creating complex shapes with high accuracy. Siliconeplus’s use of compression molding results in consistent, high-quality silicone products that meet each client’s unique specifications.
Silicone Curing Process
Curing is the process by which silicone rubber transforms into a stable, durable material. In the case of RTV (Room Temperature Vulcanizing) silicone, the material cures without heat, making it suitable for temperature-sensitive applications. Siliconeplus tailors the curing process to meet clients’ needs, ensuring each product’s durability and performance are maximized.
Silicone Mounting
Silicone mounting involves bonding silicone components to different materials or products. This is essential in industries where strong adhesion and flexibility are required. Siliconeplus provides customized mounting solutions for clients across industries, ensuring each silicone product remains secure and performs optimally under various conditions.
Benefits of Custom Silicone Solutions by Siliconeplus
At Siliconeplus, our goal is to empower our clients’ products through customized silicone solutions that provide a competitive edge. Here’s how we achieve this:
Enhanced Product Performance: Silicone is renowned for its heat resistance, anti-aging properties, flexibility, and biocompatibility. By incorporating these attributes into our clients' products, we help them achieve superior performance in demanding markets.
Tailored Designs: We understand that each client has unique requirements, so we customize our silicone solutions to meet specific needs. Whether the focus is on product durability, user experience, or innovative design, Siliconeplus’s team of engineers works closely with clients to deliver precisely what they need.
Advanced Material Integration: Siliconeplus is not limited to pure silicone; we excel at integrating silicone with other materials like metal, plastic, and FPC to create multifaceted solutions. This approach allows us to deliver products that are both functional and adaptable to various environments.
High-Quality Manufacturing Standards: From compression molding to curing and mounting, our manufacturing techniques ensure each product meets the highest quality standards. We focus on consistency and efficiency, delivering solutions that exceed client expectations.
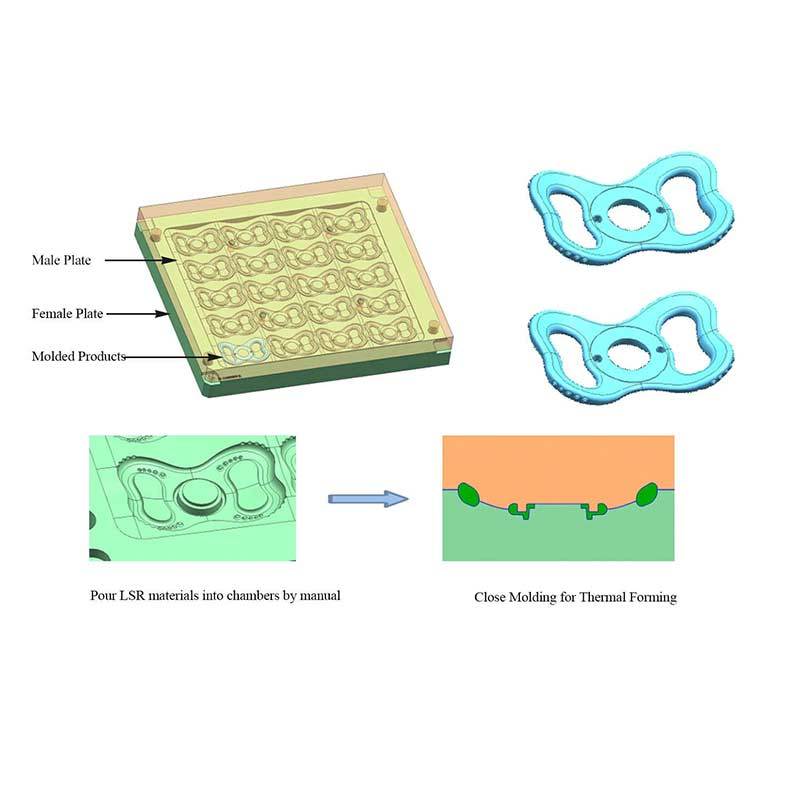