Top 5 Innovations in Custom Silicone Medical Parts for 2024
- Share
- publisher
- siliconeplus
- Issue Time
- Jul 26,2025
Summary
This article highlights 2024’s top 5 innovations in custom silicone medical parts, covering breakthroughs in biocompatibility, micro-molding, antimicrobial tech, and sustainable manufacturing
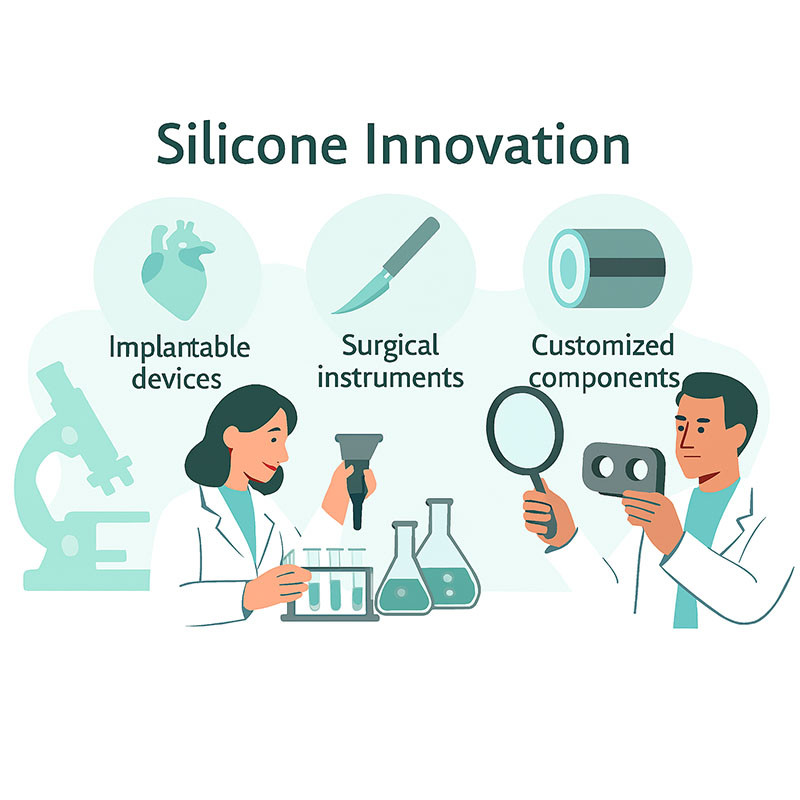
Top 5 Innovations in Custom Silicone Medical Parts for 2024
In the rapidly evolving landscape of medical device manufacturing, custom silicone parts have become a cornerstone of innovation, offering unmatched flexibility, durability, and biocompatibility. As we enter 2024, groundbreaking advancements are redefining the potential of silicone components in healthcare, from implantable devices to precision surgical instruments. Our expertise in custom silicone solutions positions us at the forefront of these developments, ensuring healthcare providers and device manufacturers stay ahead of the curve with the latest technological innovations.
1. Advanced Silicone Formulations for Superior Biocompatibility and Durability
In 2024, the development of advanced silicone formulations has revolutionized the production of medical-grade silicone components. These formulations are engineered to maximize biocompatibility, chemical resistance, and mechanical strength, making them ideal for long-term implantation and repeated sterilization cycles.
Enhanced Biocompatibility and Safety Standards
New silicone compounds incorporate non-reactive additives that reduce the risk of adverse tissue reactions, ensuring patient safety. These formulations meet rigorous standards such as ISO 10993 and USP Class VI, crucial for implantable and contact medical parts.
Improved Mechanical Properties
The latest silicone blends exhibit superior tear resistance, compression set resistance, and flexural endurance. This means custom silicone parts can withstand the demanding conditions of surgical procedures and chronic implantation without degradation, ensuring longevity and reliability.
2. Precision Micro-Molding and 3D Printing for Complex Geometries
Micro-molding and additive manufacturing techniques have unlocked new possibilities in creating highly complex, miniaturized silicone parts tailored precisely to patient-specific needs.
Micro-Molding Breakthroughs
By utilizing ultra-precise micro-molding, manufacturers can produce intricate internal channels, micro-textured surfaces, and tightly toleranced features that were previously impossible with traditional manufacturing. This process enables the production of custom silicone components such as catheter seals, valves, and sensor housings with exceptional accuracy.
3D Printing Innovation
Recent advances in silicone 3D printing facilitate rapid prototyping and small-batch production of bespoke medical parts. This technology allows design iterations to be tested swiftly, reducing time-to-market and improving design optimization.
Application Spotlight: Custom Silicone Catheters
3D printed silicone catheters with integrated microchannels support minimally invasive procedures, providing enhanced patient comfort and improved therapeutic outcomes.
Image: Silicone Micro-Molding Process
3. Smart Silicone Components with Embedded Sensors
The integration of sensors within silicone parts has propelled the development of smart medical devices capable of real-time monitoring of physiological parameters.
Embedded Sensor Technologies
Innovative conductive silicone composites enable the embedding of pressure sensors, temperature sensors, and biochemical detectors directly into custom silicone housings. These smart components facilitate continuous patient monitoring, early diagnosis, and personalized treatment plans.
Wireless Data Transmission
Coupled with miniaturized wireless modules, these sensor-embedded silicone parts transmit data seamlessly to healthcare providers, enabling remote patient management and telemedicine applications.
Use Case: Silicone-Based Wearable Sensors
Wearables made from flexible silicone with embedded sensors are now capable of tracking vital signs such as heart rate, respiratory rate, and oxygen saturation with high accuracy.
Image: Silicone Embedded Sensor Device
4. Antimicrobial and Self-Cleaning Silicone Technologies
Infection control remains paramount in medical environments. The advent of antimicrobial silicone coatings and self-cleaning surfaces for custom medical parts significantly reduces biofilm formation and pathogen transmission.
Antimicrobial Additives
Incorporating silver nanoparticles, copper ions, or quaternary ammonium compounds into silicone matrices creates long-lasting antimicrobial properties. These bioactive surfaces inhibit bacterial growth, lowering the risk of hospital-acquired infections.
Self-Cleaning Surfaces
Photocatalytic coatings activated by light exposure enable self-cleaning of silicone components, reducing the need for frequent sterilization and maintenance. These surfaces are ideal for surgical instruments, implant covers, and hospital equipment.
Impact on Healthcare Settings
The synergy of antimicrobial and self-cleaning features in custom silicone parts enhances patient safety, reduces costs, and streamlines hospital workflows.
Image: Antimicrobial Silicone Surface
5. Eco-Friendly and Sustainable Silicone Manufacturing
Sustainability in medical device manufacturing has gained critical importance. Eco-conscious silicone production leverages renewable raw materials, low-impact processes, and recyclable components.
Green Raw Materials
Manufacturers are now utilizing bio-based silicones derived from renewable sources, significantly reducing carbon footprint while maintaining medical-grade quality.
Energy-Efficient Processes
Innovations in energy-efficient curing and waste reduction during manufacturing lower environmental impact, aligning with global sustainability goals.
Recyclable and Reusable Silicone Parts
Developing recyclable silicone composites and refurbishment protocols ensures circular economy principles are integrated into medical silicone part production.
Industry Impact
Adopting sustainable silicone solutions not only fulfills regulatory and ethical standards but also enhances brand reputation and market competitiveness.
Conclusion: The Future of Custom Silicone Medical Parts in 2024 and Beyond
The top five innovations outlined above exemplify the transformative power of silicone technology in healthcare. From advanced material formulations to smart, antimicrobial, and sustainable solutions, the trajectory of custom silicone medical parts is set to redefine patient care, improve device performance, and streamline manufacturing processes.
As industry leaders, we remain committed to driving innovation, adhering to the highest standards, and delivering bespoke silicone solutions tailored to the evolving needs of global healthcare. The future of medical silicone parts is not only promising but also pivotal in shaping more effective, safer, and sustainable healthcare systems worldwide.
Contact us today to explore how our cutting-edge custom silicone solutions can elevate your medical device manufacturing in 2024 and beyond.