The Role of Custom Silicone in Medical Device Waterproofing
- Share
- publisher
- siliconeplus
- Issue Time
- Jul 21,2025
Summary
Custom silicone offers superior waterproofing for medical devices with biocompatibility, durability, and precision sealing—ensuring safety, longevity, and regulatory compliance.
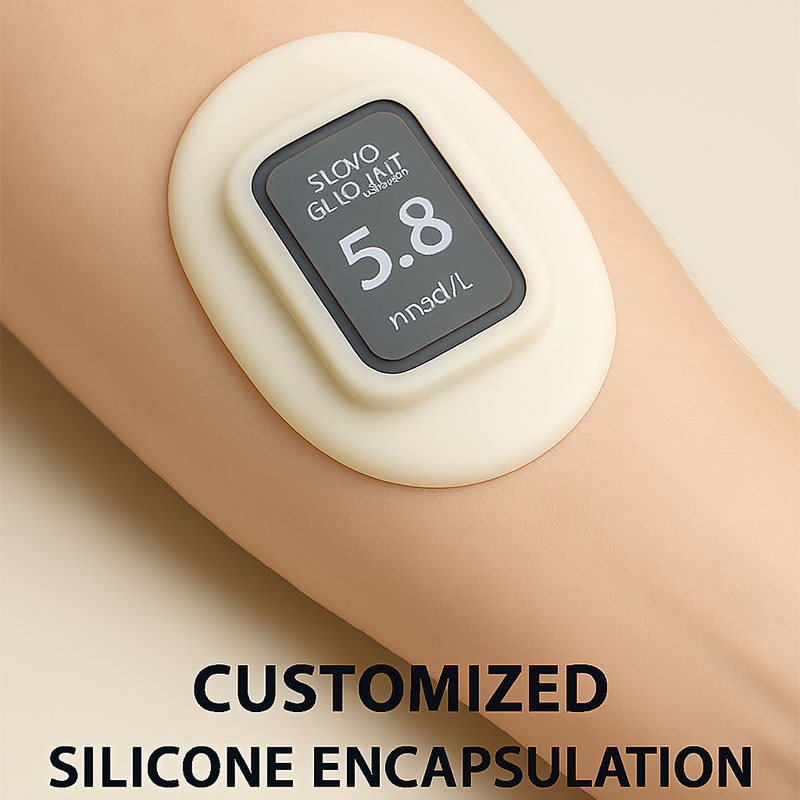
The Role of Custom Silicone in Medical Device Waterproofing
Introduction: Elevating Medical Device Reliability with Custom Silicone Solutions
In the rapidly advancing field of healthcare technology, medical devices are becoming increasingly sophisticated, integrating complex electronics, sensors, and delicate components. Ensuring their reliability and longevity hinges significantly on effective waterproofing solutions. Among the myriad of materials available, custom silicone stands out as the pinnacle choice for waterproofing medical devices due to its versatility, biocompatibility, and robust protective properties.
Our commitment to delivering tailored silicone solutions ensures that each device's unique specifications are met with precision-engineered formulations. This comprehensive guide delves into the critical role that custom silicone plays in medical device waterproofing, exploring material properties, application techniques, compliance standards, and innovative advancements shaping the future of healthcare protection.
Understanding Custom Silicone: The Foundation for Superior Waterproofing
What Is Custom Silicone and Why Is It Essential?
Custom silicone refers to engineered silicone formulations designed specifically to meet the unique requirements of a particular medical device. Unlike generic silicone sealants, customized formulations are tailored in terms of viscosity, adhesion properties, elasticity, biocompatibility, and chemical resistance.
Key advantages of custom silicone include:
- Exact fit for device geometries
- Enhanced durability and flexibility
- Optimized curing times
- Compliance with medical standards
- Improved resistance to bodily fluids and cleaning agents
Material Properties that Make Custom Silicone Ideal for Medical Waterproofing
Property | Description | Impact on Waterproofing |
---|---|---|
Biocompatibility | Meets ISO 10993 standards | Safe for direct contact with human tissue and fluids |
Chemical Resistance | Resistant to disinfectants, bodily fluids, and cleaning agents | Maintains integrity over time |
Elasticity & Flexibility | Maintains seal integrity under mechanical stress | Prevents cracks and leaks during device movement |
Thermal Stability | Operates effectively across a wide temperature range | Ensures performance in various clinical environments |
Transparency | Clear formulations available | Facilitates inspection and internal visibility |
Critical Role of Custom Silicone in Medical Device Waterproofing
Achieving Perfect Seals in Complex Geometries
Medical devices often feature intricate designs, including small cavities, tight joints, and delicate electronic components. Custom silicone formulations are engineered to conform precisely to these geometries, ensuring comprehensive sealing without gaps or weak points.
Advanced application techniques, such as dispensing robots and precision moldings, allow for consistent and uniform application of silicone, resulting in reliable waterproof barriers that withstand daily sterilization cycles and mechanical stresses.
Enhanced Durability and Long-Term Performance
The long-term integrity of waterproof seals is paramount in medical applications. Custom silicone formulations are designed to resist aging, UV exposure, and chemical degradation, ensuring consistent protection over the device's lifespan.
For example, medical-grade silicone exhibits superior elasticity, preventing cracks or degradation even after repeated sterilization procedures, such as autoclaving or chemical sterilization.
Biocompatibility and Regulatory Compliance
In the healthcare sector, safety standards are non-negotiable. Custom silicone solutions are formulated to meet or exceed standards such as ISO 10993, USP Class VI, and FDA approvals. This guarantees that sealants do not provoke adverse tissue reactions and are safe for patient contact.
Application Techniques for Custom Silicone in Medical Waterproofing
Precision Dispensing and Molding
Utilizing automated dispensing systems, custom silicone can be applied with micrometer accuracy, ensuring consistent coverage. Molding techniques allow for integral seals that are integrated into the device’s structure, reducing assembly time and enhancing seal strength.
Regulatory and Quality Assurance in Silicone Waterproofing
Compliance with International Standards
Medical device manufacturers must adhere to stringent standards. Custom silicone solutions are certified to meet ISO 13485, ISO 10993, USP Class VI, and FDA regulations. These certifications attest to the material's safety, biocompatibility, and performance.
Testing and Validation
Comprehensive testing protocols include:
- Leak testing under pressure differentials
- Accelerated aging tests
- Chemical resistance assessments
- Mechanical stress evaluations
- Sterilization cycle testing
Innovations Driving the Future of Medical Silicone Waterproofing
Smart Silicone Sealants
Emerging smart silicone materials incorporate self-healing properties, antimicrobial agents, or sensor integration for real-time leak detection. These innovations enhance device safety and maintenance, reducing downtime and recall risks.
3D Printing with Custom Silicone
Advances in additive manufacturing enable complex silicone components to be printed precisely, facilitating rapid prototyping and customized seals tailored to specific device architectures.
Case Studies: Success Stories of Custom Silicone Waterproofing
High-Precision Wearables
Smart medical wearables, such as continuous glucose monitors, rely on custom silicone encapsulation to protect sensitive electronics from moisture ingress while maintaining flexibility and skin comfort.
Implantable Devices
Implantable cardiac devices utilize biocompatible silicone seals with long-lasting waterproof properties, ensuring device functionality over years of implantation.
Diagnostic Equipment
Portable ultrasound devices and lab analyzers employ custom silicone gaskets to withstand harsh cleaning protocols and environmental exposure, maintaining accuracy and reliability.
Conclusion: Custom Silicone—The Ultimate Waterproofing Solution for Medical Devices
Custom silicone is undeniably the cornerstone of effective waterproofing in medical devices. Its tailor-made properties—from biocompatibility and chemical resistance to mechanical durability—make it the ideal material for safeguarding sensitive components in diverse clinical environments.
By leveraging advanced formulations, precise application techniques, and strict adherence to regulatory standards, we can ensure the highest levels of protection, device longevity, and patient safety. The continuous innovation in medical-grade silicone technology promises a future where medical devices are more reliable, more durable, and more adaptable than ever before.