Silicone Molds: What is the Process from Injection Molding to Custom Silicone Products?
- Share
- publisher
- Siliconeplus Editor
- Issue Time
- Nov 14,2024
Summary
Silicone is valued for its flexibility, and biocompatibility. Siliconeplus excels in custom silicone injection molding, providing tailored solutions that improve product performance and longevity.
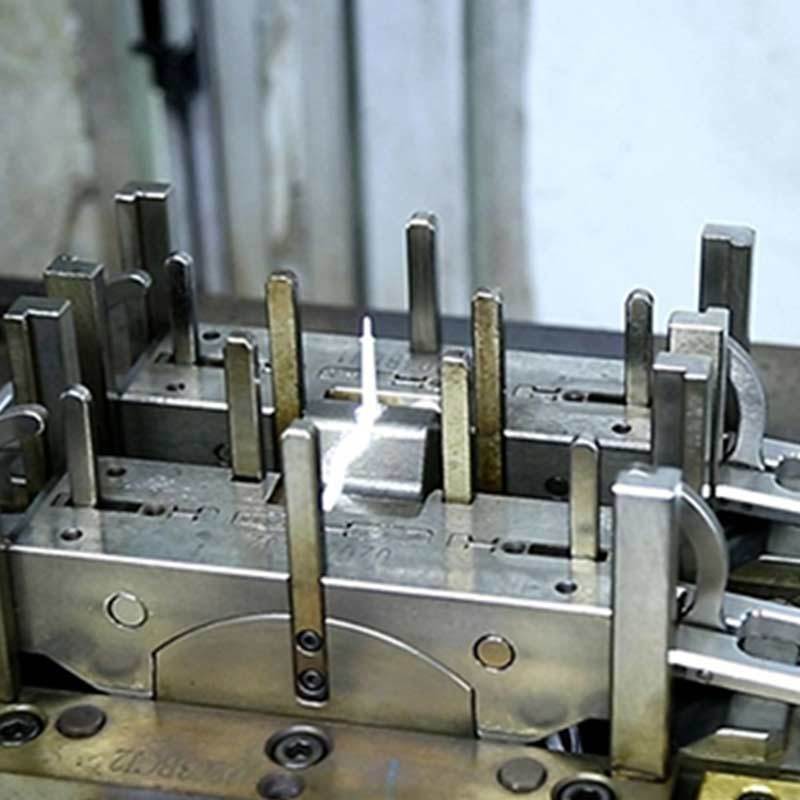
Silicone is a versatile material widely used in various industries for its unique properties such as flexibility, durability, high-temperature resistance, and biocompatibility. From medical devices to automotive parts, silicone molds play a crucial role in creating custom silicone products that meet specific performance requirements. At Siliconeplus, we specialize in designing and manufacturing custom silicone products using advanced injection molding techniques, offering tailored solutions that enhance the functionality and durability of your products.
In this article, we’ll walk you through the process of silicone molding, from injection molding to custom silicone products, providing you with a deeper understanding of how this technology works and how it can benefit your business.
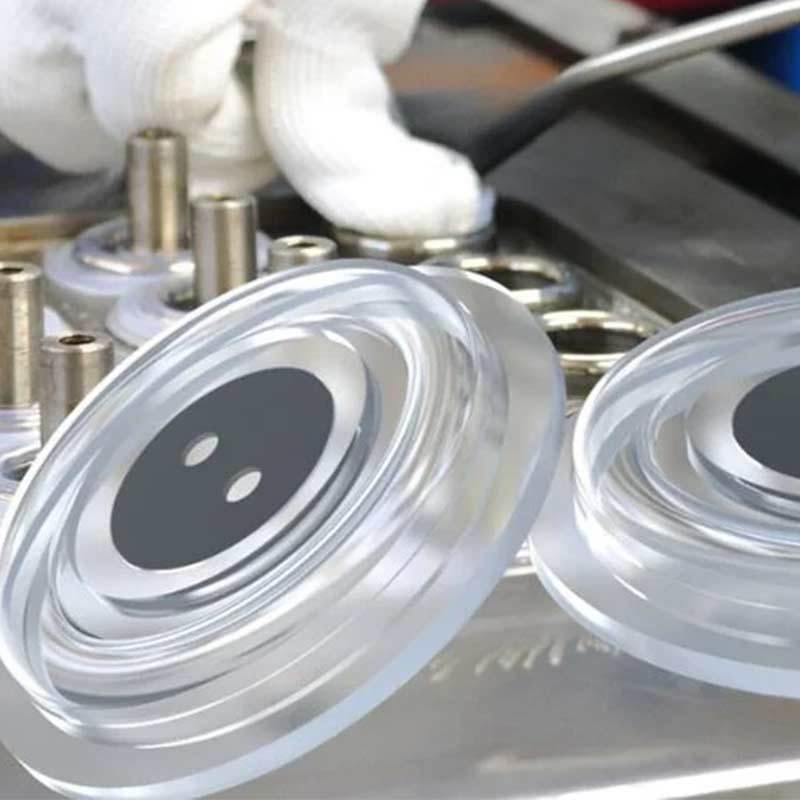
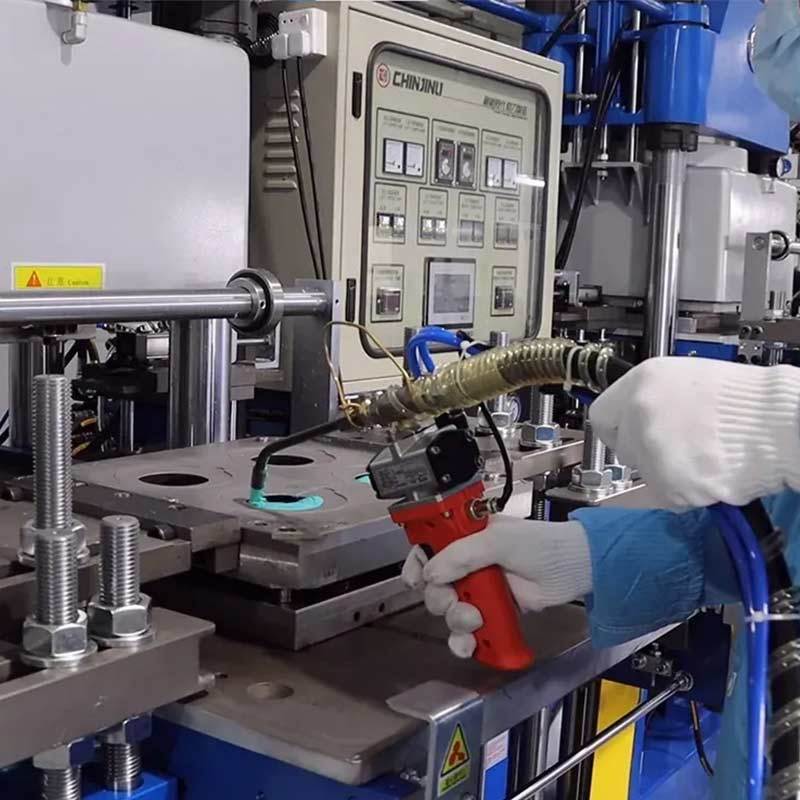
What is Silicone Injection Molding?
Injection molding is a manufacturing process that involves injecting molten material into a mold cavity under high pressure. For silicone products, this process uses Liquid Silicone Rubber (LSR), a high-performance material known for its flexibility, high-temperature resistance, and ability to withstand environmental stressors.
The process begins by heating the silicone rubber until it becomes a liquid. Once the silicone reaches the required viscosity, it is injected into a mold cavity where it cools and solidifies into the desired shape. This process allows for high precision and the production of complex geometries, making it ideal for manufacturing silicone products with intricate details, such as seals, gaskets, or medical devices.
Step 1: Designing the Mold for Silicone Molding
Before any molding can take place, a custom mold design is required. The design phase is critical because the mold serves as the blueprint for the final product. At Siliconeplus, we work closely with our clients to understand their needs and tailor the mold design to their specifications. During this phase, we consider the following factors:
Material Properties: Different silicone formulations may be required depending on the end-use of the product. Whether it's medical-grade silicone, food-safe silicone, or high-performance silicone for industrial applications, the right formulation must be chosen.
Part Geometry: The complexity of the product’s design affects the mold design. For instance, products with intricate features or undercuts may require more advanced tooling techniques.
Production Volume: The intended production volume plays a role in determining the type of mold to use. For low to medium volumes, aluminum molds may be used, whereas for higher volumes, steel molds are preferred for their durability and longevity.
Once the mold design is finalized, it is sent to the mold-making department for the creation of a high-quality mold tool.
Step 2: Injection Molding Process
With the mold ready, the injection molding process begins. The Liquid Silicone Rubber (LSR) is first prepared and heated to the appropriate temperature. The silicone is then injected into the mold cavity under high pressure using an injection molding machine. The machine is designed to handle the high viscosity of liquid silicone and ensure that the silicone fills every part of the mold cavity.
Key steps in this stage include:
Injection: The LSR is injected into the mold under high pressure.
Cooling: After the mold is filled, the silicone is allowed to cool and solidify. This step ensures the product takes the exact shape and texture of the mold cavity.
Demolding: Once the silicone has cooled and solidified, the mold is opened, and the product is carefully removed.
This process is repeatable, which makes it ideal for producing large quantities of identical silicone products with consistent quality.
Step 3: Post-Processing and Customization
After the initial molding process, additional steps are often required to ensure the final product meets the desired quality and performance standards. These post-processing steps include:
Trimming and Flash Removal: Excess silicone, known as flash, may form along the edges of the mold. This is removed during trimming, ensuring the product is smooth and clean.
Curing: Depending on the type of silicone used, the product may undergo additional curing to enhance its physical properties. This process ensures that the silicone is fully set and reaches its optimum strength and elasticity.
Custom Color and Texture: Custom silicone products can be made in a variety of colors, finishes, and textures. Whether it’s a matte, glossy, or soft-touch finish, silicone can be customized to meet your aesthetic and functional needs.
Adding Other Materials: For enhanced functionality, other materials such as metal, plastic, or FPC (Flexible Printed Circuit boards) may be integrated into the silicone during the molding process. This is especially common in applications like automotive components or medical devices where additional strength or electronics integration is required.
Step 4: Quality Control and Testing
At Siliconeplus, we take quality seriously. Each batch of silicone products undergoes rigorous quality control to ensure they meet both client specifications and industry standards. Our quality control processes include:
Dimensional Checks: Every product is measured to ensure that it meets the required specifications.
Material Testing: We test the silicone material for key properties such as tensile strength, tear resistance, and flexibility.
Functionality Testing: For products used in critical applications (e.g., automotive parts or medical devices), additional functional tests are performed to ensure that the product will perform reliably under real-world conditions.
Compliance with Industry Standards: For products used in regulated industries, such as medical or food-related products, we ensure compliance with certifications like ISO 13485 and FDA standards.
Step 5: Final Packaging and Delivery
Once the silicone products pass all tests, they are carefully packaged and prepared for delivery. We offer flexible packaging options based on your requirements, whether you need individual packaging or bulk packaging for larger orders. Our goal is to ensure that the products arrive at their destination in perfect condition.
Benefits of Silicone Overmolding
Versatility: Silicone can be combined with metals, plastics, and other materials to create high-performance, custom products that meet the specific needs of the automotive, medical, consumer electronics, and other industries.
Durability: Silicone is known for its long-lasting performance, even in harsh environments. It’s resistant to heat, chemicals, and UV rays, making it an ideal choice for automotive and industrial applications.
Customization: Silicone allows for a high degree of customization, both in terms of design and functionality. Whether you need a specific color, texture, or integration with other materials, silicone can be molded to fit your exact requirements.
Conclusion
The process of creating custom silicone products using injection molding involves several key steps, from the initial mold design to the final testing and delivery of the product. Siliconeplus is dedicated to providing our clients with high-quality silicone products tailored to meet their specific needs. By using advanced injection molding techniques and combining silicone with other materials like metal and plastic, we can create durable, reliable, and high-performance products for a variety of industries, including automotive, medical, and consumer electronics.
If you are interested in learning more about our custom silicone solutions or would like to discuss your project, don’t hesitate to contact us. Our team of experts is ready to help you achieve your product goals with precision and innovation.