Liquid Silicone Rubber Injection Molding: A Detailed Guide
- Share
- publisher
- Siliconeplus Editor
- Issue Time
- Jan 20,2025
Summary
Liquid silicone rubber (LSR) injection molding offers superior flexibility, and precision over traditional rubber, making it ideal for medical, automotive, and consumer products manufacturing.
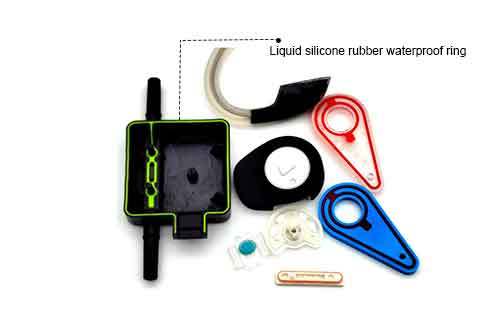
Liquid silicone rubber (LSR) injection molding is a game-changer in industries like automotive, medical, and consumer goods. But what exactly makes it unique, and why is it becoming the preferred choice for manufacturers?
Liquid silicone rubber is a versatile material, offering flexibility, durability, and high-performance properties. It is different from traditional rubber silicone in its processing and application advantages.
Whether you're designing medical devices or automotive parts, understanding how liquid silicone rubber injection molding works can revolutionize your product development process. Let's dive deeper into the key differences between liquid silicone and rubber silicone.
What is the difference between liquid silicone and rubber silicone?
The terms "liquid silicone" and "rubber silicone" often get mixed up, but they are distinct materials with unique properties. Let's break down these differences to help you choose the right one for your product.
Liquid silicone is in a liquid state and is ideal for injection molding, while rubber silicone is typically a solid or semi-solid form used in other types of manufacturing processes.
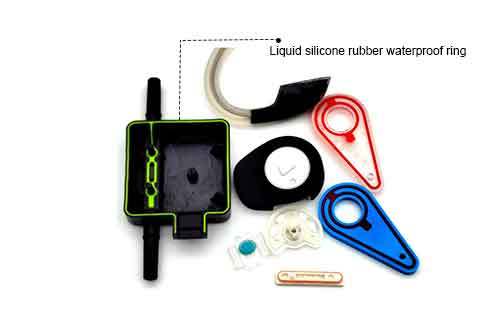
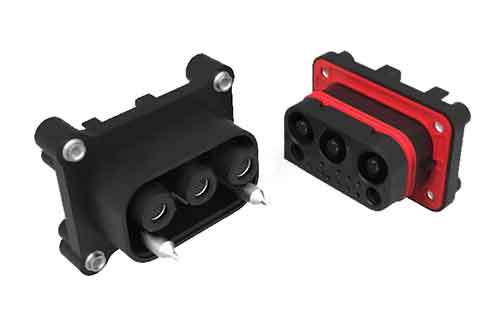
Liquid Silicone vs Rubber Silicone: Key Characteristics
Liquid silicone rubber is a high-performance elastomer in its liquid form that is perfect for injection molding. It has properties like high-temperature resistance, biocompatibility, and flexibility, making it suitable for applications like medical devices and seals.
On the other hand, rubber silicone generally refers to solid or semi-solid forms, often used for compression molding. While it shares some similarities with LSR, its manufacturing process and use cases can differ significantly. Rubber silicone is often more durable in extreme conditions, while liquid silicone offers more precision in molding.
Feature | Liquid Silicone Rubber (LSR) | Rubber Silicone |
State | Liquid | Solid/Semi-solid |
Molding Process | Injection Molding | Compression Molding |
Temperature Resistance | High | High |
Flexibility | Very Flexible | Less Flexible |
Biocompatibility | Excellent | Good |
What are the advantages of liquid silicone rubber injection molding?
Why is LSR injection molding the go-to method for many industries? Let’s explore the specific advantages that make it a top choice for manufacturers.LSR injection molding offers advantages like high precision, biocompatibility, resistance to harsh conditions, and the ability to create complex designs with minimal waste.
Key Benefits of LSR Injection Molding
Key Benefits of LSR Injection Molding
High Precision and Flexibility: LSR injection molding allows for precise, high-quality parts to be produced with excellent repeatability. This makes it ideal for complex, intricate designs often required in industries like medical and automotive.
Durability and Temperature Resistance: Liquid silicone rubber can withstand extreme temperatures and harsh environments. Its ability to endure both heat and cold without degrading makes it highly valuable for products exposed to varying climates.
Cost-Effectiveness and Minimal Waste: Injection molding processes are efficient, and LSR injection molding in particular offers low waste due to its precise mold filling. This reduces material usage and production costs.
Biocompatibility: Liquid silicone rubber is non-toxic, making it ideal for medical applications like implants and devices that come into contact with the human body.
How long does it take for liquid silicone rubber to cure?
Curing time is a crucial factor in manufacturing. How long does liquid silicone rubber take to cure in injection molding processes? Let’s find out.
The curing time for liquid silicone rubber is typically fast, with most components requiring around 10-30 seconds, depending on the part size and molding conditions.
Understanding Curing Time in LSR Molding
Curing time is a key variable in the LSR injection molding process. The curing process, also known as vulcanization, ensures that the silicone rubber reaches its final state. Most LSR components are cured within 10-30 seconds, though the exact time depends on factors like:
Part Thickness: Thicker parts take longer to cure.
Mold Temperature: A hotter mold speeds up curing time.
Material Properties: Different LSR formulations may require more or less curing time.
With advancements in equipment and processes, manufacturers can optimize curing times for better efficiency.
Can silicone be injection molded?
Yes, silicone can be injection molded. But how does this process differ from other forms of molding, and why is it ideal for silicone materials? Let’s explore.Silicone is an ideal material for injection molding due to its ability to maintain its properties under high temperature and pressure, resulting in high-quality, durable products.
Why Silicone is Ideal for Injection Molding
Silicone is uniquely suited to injection molding due to its excellent flow properties in a liquid state, allowing it to fill complex molds with precision. This makes it an attractive option for industries requiring:
High-Performance Components: Like seals, gaskets, and medical devices.
Complex Designs: With intricate shapes and fine details.
Consistency: Ensuring every piece meets the same high standards.
Injection molding with silicone ensures a reliable, repeatable process, which is essential for mass production.
Conclusion
Liquid silicone rubber injection molding offers incredible precision, flexibility, and durability, making it a top choice for industries requiring high-performance products.