How to Make Silicone Products?
- Share
- publisher
- Siliconeplus Editor
- Issue Time
- Oct 25,2024
Summary
Custom silicone product manufacturing involves material preparation, mold design, and molding processes like compression or injection molding to shape and cure the silicone.

How to Make Silicone Products??
Making custom silicone products involves a series of steps that depend on the type of product being manufactured. Below is a general outline of the process, typically followed by a silicone product manufacturer.
1. Material Preparation
Silicone Rubber: Start with high-quality silicone rubber, either in liquid or solid form, depending on the custom silicone product specifications. The silicone may be mixed with additives to improve properties such as flexibility, durability, heat resistance, or color.
Coloring: Silicone can be pre-colored by adding pigments or can be clear, depending on the product requirements.
2. Mold Design and Fabrication
Custom Mold Creation: Design the mold based on the specific custom silicone products being manufactured. This mold can be made of aluminum, steel, or other materials that can withstand the high temperatures used in silicone molding.
Mold Types:
Compression Molding: A mold is filled with uncured silicone, and heat and pressure are applied to shape it.
Injection Molding: Liquid silicone rubber (LSR) is injected into a mold cavity, where it cures and forms the product.
Extrusion: Silicone is forced through a die to create long, continuous shapes like tubing or profiles.
3. Molding Process
Compression Molding Process:
Place pre-measured pieces of uncured silicone rubber into the mold.
Close the mold and apply heat and pressure.
After the silicone has cured (vulcanized), the mold is opened, and the product is removed.
Injection Molding Process:
Liquid silicone is injected into the mold at high pressure.
Heat is applied to cure the silicone inside the mold.
Once cured, the product is ejected from the mold.
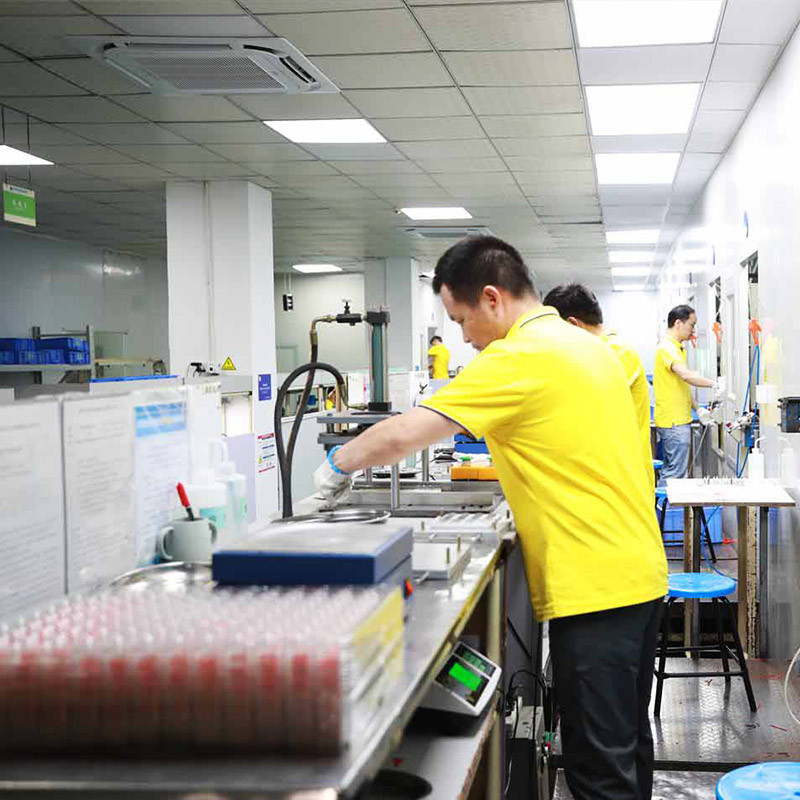

5. Post-Processing
Trimming and Deflashing: After the silicone product is removed from the mold, any excess material (flash) is trimmed or deflashed.
Surface Treatment: Some custom silicone products may undergo surface treatments such as coating with oils or powders to improve texture or feel.
Additional Assembly: For products with multiple components, additional assembly may be needed, such as bonding silicone to other materials like metal or plastic.
6. Quality Control and Testing
Inspection: Custom silicone products are inspected for defects such as bubbles, cracks, or improper curing.
Testing: Depending on the application, products may undergo additional tests such as tensile strength, durability, heat resistance, or flexibility tests.
7. Finishing and Packaging
The finished product may receive additional finishing processes like painting, labeling, or adding logos, often tailored to the specific needs of the client ordering custom silicone products.
Finally, the products are packaged according to customer specifications and prepared for shipment.
Common Methods for Silicone Manufacturing:
Compression Molding: Ideal for thicker or more solid silicone products like silicone seals, gaskets, or baby toys.
Injection Molding: Best for high-precision parts, like medical silicone devices or electronics.
Extrusion: Used for creating continuous silicone forms like tubes, cables, or strips.
Advantages of Custom Silicone Products:
High Temperature Resistance: Silicone can withstand extreme heat and cold.
Flexibility and Durability: Silicone is highly flexible and long-lasting.
Biocompatibility: It's safe for medical, baby products, and food contact applications.
Customizability: Custom silicone products can be easily molded into complex shapes and customized with colors and designs.
A silicone product manufacturer plays a crucial role in ensuring that every custom silicone product is crafted to meet specific standards, whether for industrial, medical, or consumer use. By following the above steps, manufacturers can produce a wide range of high-quality silicone products, fully customizable to meet the demands of diverse industries.
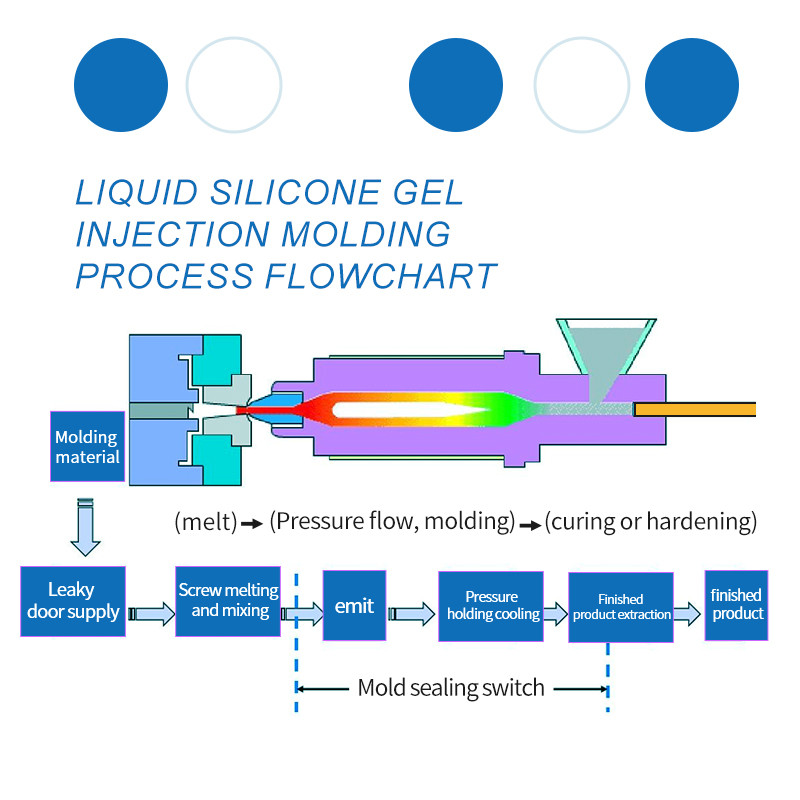