How Silicone Overmolding Enhances the Anti-Leak Features of Eye Cream Applicators
- Share
- publisher
- siliconeplus
- Issue Time
- Jul 15,2025
Summary
Silicone overmolding enhances eye cream applicators with anti-leak sealing, durability, and luxury feel, boosting product safety, user experience, and brand value in premium skincare packaging.
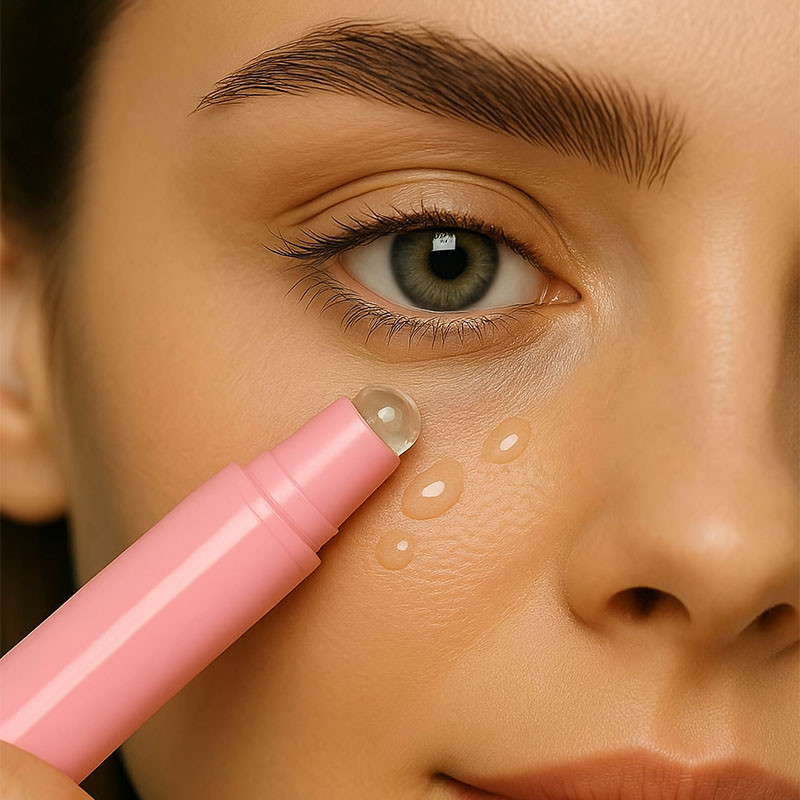
How Silicone Overmolding Enhances the Anti-Leak Features of Eye Cream Applicators
In the highly competitive skincare industry, product integrity and user experience are paramount. Among the myriad of innovations that elevate product performance, silicone overmolding has emerged as a game-changer, particularly in the design of eye cream applicators. This advanced manufacturing process not only enhances the anti-leak properties of applicators but also elevates the overall luxury feel, durability, and safety of cosmetic packaging.
Understanding Silicone Overmolding: A Breakthrough in Cosmetic Packaging
Silicone overmolding involves the process of applying a silicone elastomer layer over a substrate, such as plastic or metal components of an eye cream applicator. This technique creates a seamless, flexible, and durable coating that conforms precisely to the underlying structure, offering numerous benefits:
- Enhanced sealing capabilities
- Superior flexibility and resilience
- Improved tactile experience
- Resistance to environmental factors such as temperature and humidity
By integrating silicone overmolding into eye cream applicator manufacturing, brands can deliver products that are not only leak-proof but also more aesthetically appealing and user-friendly.
The Critical Role of Anti-Leak Features in Eye Cream Applicators
Leakage in eye cream dispensers can compromise product integrity, cause messes, and diminish consumer confidence. Traditional applicators often suffer from poor sealing, material degradation, or manufacturing inconsistencies, leading to product wastage and hygiene concerns.
Anti-leak features are essential to:
- Maintain product freshness
- Prevent contamination
- Ensure precise dosage control
- Enhance user safety and satisfaction
The application of silicone overmolding directly addresses these issues by creating impermeable seals and flexible barriers that adapt to usage stresses, thus minimizing leak risks.
How Silicone Overmolding Boosts Anti-Leak Performance
1. Superior Sealing and Flexibility
Silicone’s exceptional elasticity allows it to form tight seals around complex geometries of applicators. Unlike rigid materials, silicone can absorb and adapt to pressure variations during use, preventing fluid escape even under rigorous handling.
2. Seamless and Precise Coating
The overmolding process ensures uniform coverage over the applicator's components, eliminating gaps or seams where leaks could originate. This continuous barrier significantly reduces the possibility of micro-leaks that compromise product safety.
3. Resistance to Environmental Stressors
Silicone’s chemical stability and temperature resistance mean that the anti-leak seals remain intact in diverse conditions—be it during transportation, storage, or daily use. This durability ensures long-term leak prevention.
4. Enhanced Mechanical Strength
The flexible yet resilient nature of silicone overmolds provides additional mechanical protection, preventing cracks or deformation that might lead to leaks. This robustness is especially critical for portable, travel-friendly applicators.
5. Improved User Experience
The soft, rubber-like texture of silicone enhances grip and handling, reducing accidental drops or mishandling that could cause leaks. Additionally, the aesthetic appeal of silicone coatings lends a luxury feel that appeals to discerning consumers.
Manufacturing Process of Silicone Overmolding for Eye Cream Applicators
The process involves several precise steps:
Design and Mold Preparation:
CAD models are created to define the applicator's geometry, ensuring optimal placement of the silicone layer for sealing and grip.Injection of Base Material:
The core applicator—typically made of plastic or metal—is manufactured with high precision.Silicone Overmolding:
The silicone elastomer is injected over the pre-formed applicator using state-of-the-art injection molding machines. The process involves controlled temperature and pressure to ensure uniform adhesion and coating thickness.Curing and Finishing:
The silicone is cured in dedicated ovens, resulting in a solid, elastic coating. Post-processing includes inspection, trimming, and quality testing to verify leak-proof performance.Assembly and Packaging:
The overmolded applicators are assembled with other components, tested for leakage and durability, then packaged for distribution.
Advantages of Silicone Overmolding in Eye Cream Applicator Design
Feature | Benefit | Impact on Product Performance |
---|---|---|
Enhanced Seal Integrity | Prevents fluid escape | Ensures product remains uncontaminated and fresh |
Superior Flexibility | Absorbs usage stresses | Maintains leak-proof status over time |
Chemical and Temperature Resistance | Withstands environmental factors | Reduces risk of seal degradation |
Aesthetic and Tactile Appeal | Luxurious soft-touch finish | Improves consumer satisfaction and brand perception |
Durability and Mechanical Strength | Resists cracking and deformation | Prolongs product lifespan and reduces returns |
Case Study: Premium Eye Cream Applicator with Silicone Overmolding
A leading skincare brand integrated silicone overmolding into their luxury eye cream applicator. The results included:
- Zero leak incidents over a 12-month testing period
- Enhanced user feedback citing improved grip and feel
- Reduced product wastage due to improved sealing
- Elevated brand perception as a provider of innovative, high-quality packaging
This case exemplifies the transformative impact of silicone overmolding on product safety, functionality, and consumer appeal.
Conclusion: Elevating Eye Cream Packaging with Silicone Overmolding
The application of silicone overmolding technology in the design of eye cream applicators represents a significant advancement in skincare packaging engineering. By providing superior anti-leak features, enhanced durability, and luxurious tactile qualities, this process addresses the core challenges faced by cosmetic brands aiming for premium product delivery.
In an industry where trust, safety, and aesthetic appeal are critical, silicone overmolding offers an unmatched solution that outperforms traditional sealing methods. As consumer expectations continue to rise, adopting this innovative manufacturing process will position brands at the forefront of luxury skincare innovation.
Trust in the power of silicone overmolding to redefine your skincare packaging—delivering leak-proof, durable, and luxurious eye cream applicators that meet the highest standards of quality and consumer satisfaction.