Empowering Innovation with Silicone Technology – Welcome to 2025 with Siliconeplus
- Share
- publisher
- Siliconeplus Editor
- Issue Time
- Feb 6,2025
Summary
Silicone injection molding is an efficient, automated process producing high-precision, complex silicone parts with excellent material properties, widely used in medical, automotive.
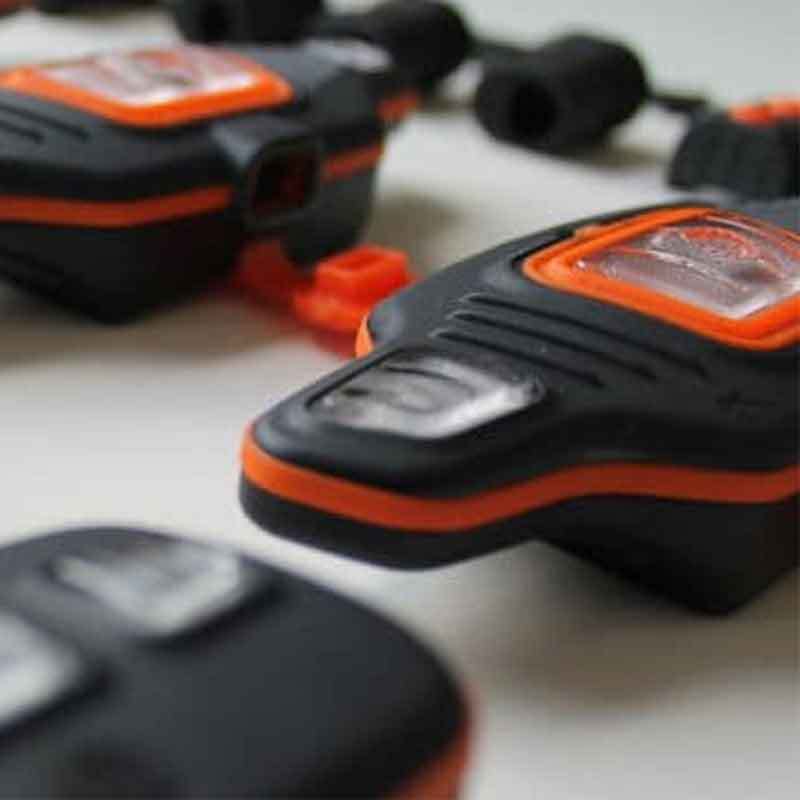
Silicone injection molding is an advanced manufacturing process widely used across medical, electronics, automotive, baby products, and consumer electronics industries. This technique involves injecting liquid silicone rubber (LSR) into a mold cavity, where it is cured under high temperature and pressure to produce silicone products with complex shapes and excellent performance.
The main advantages of silicone injection molding include:
High Precision and Complex Shapes
Injection molding technology can meet the needs of complex product designs, producing silicone parts with rich details and precise dimensions. Compared to traditional compression molding, injection molding offers better product consistency and repeatability.
Efficient Automated Production
Injection molding equipment is highly automated, with short production cycles suitable for large-scale manufacturing, significantly improving efficiency and reducing labor costs.
Excellent Material Properties
Liquid silicone possesses outstanding high and low temperature resistance, biocompatibility, non-toxicity, chemical resistance, and elasticity, making it ideal for applications requiring high performance and safety.
Eco-friendly and Energy-saving
The liquid silicone injection molding process generates minimal waste, and the equipment is energy-efficient and environmentally friendly, aligning with modern green manufacturing trends.
Versatile Applications
Injection molding can produce a wide range of silicone products including baby nipples, medical catheters, seals, electronic buttons, and automotive parts, catering to diverse industry demands.
In practical production, multiple key parameters must be controlled in silicone injection molding:
Mold Design
Mold design must consider flow path layout, venting systems, and cooling channels to ensure smooth filling and uniform curing of liquid silicone, preventing product defects.
Injection Temperature and Pressure
Proper temperature and pressure ensure quick and uniform filling of the mold, improving mechanical properties and surface quality of the products.
Curing Time
Reasonable curing time guarantees complete cross-linking of silicone, enhancing product durability and elasticity.
With continuous advancements in material science and equipment technology, silicone injection molding is evolving toward higher efficiency, precision, and environmental sustainability. Companies are driving innovation and meeting diverse market needs by optimizing formulations, improving mold manufacturing techniques, and enhancing automation levels.
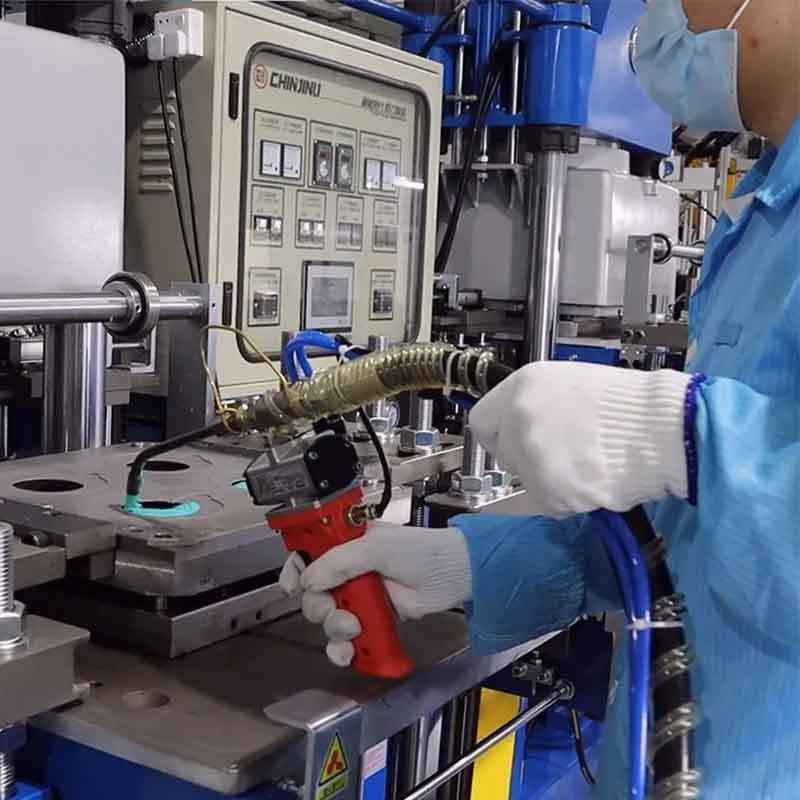
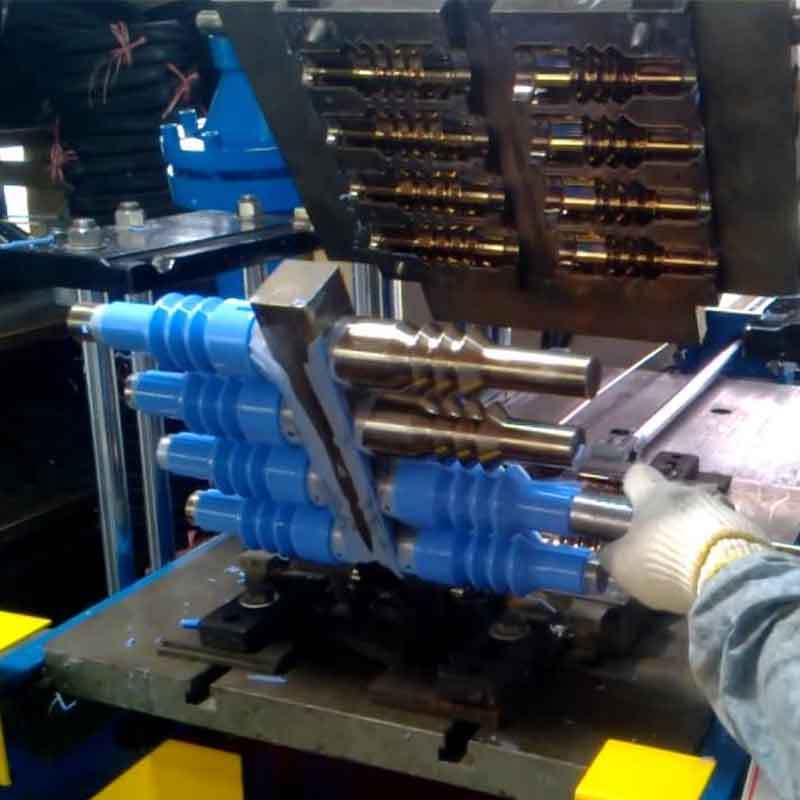
Why Choose Silicone Injection Moulding for Your Silicone Parts?
At Siliconeplus, we utilize advanced silicone injection molding techniques to produce high-performance silicone parts with:
High-temperature resistance – ensuring durability in extreme environments.
Aging resistance – enhancing product lifespan.
Superior flexibility & biocompatibility – perfect for medical, industrial, and electronic applications.
With 23 years of experience, we specialize in precision silicone injection moulding, combining silicone with metal, plastic, and FPC to meet diverse industry needs.