Designing for Cleanability: Custom Silicone Parts in Medical Devices
- Share
- publisher
- siliconeplus
- Issue Time
- Jul 25,2025
Summary
This article explores how custom silicone parts improve cleanability in medical devices through smart design, surface optimization, and material selection, regulatory compliance.
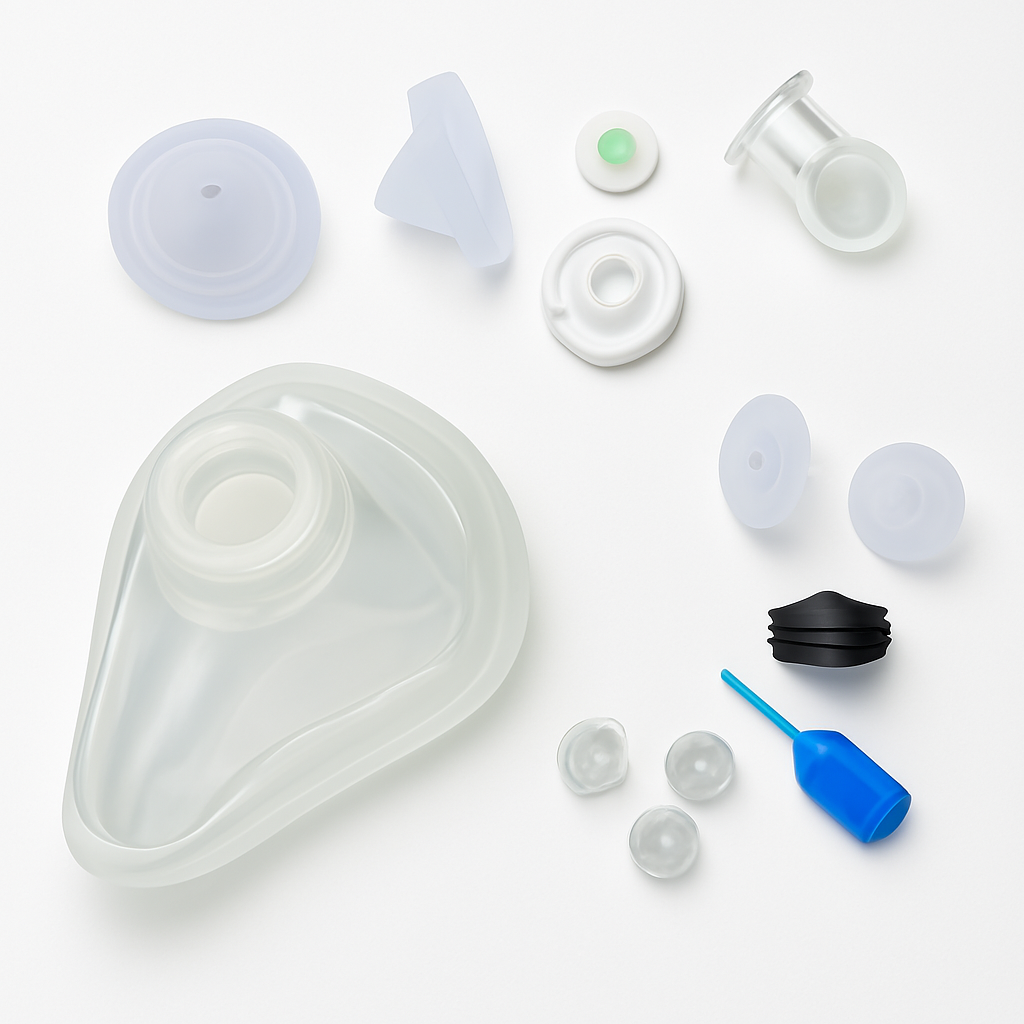
Designing for Cleanability: Custom Silicone Parts in Medical Devices
Introduction: The Critical Role of Cleanability in Medical Device Design
In the rapidly evolving landscape of healthcare technology, medical devices must adhere to the highest standards of hygiene, safety, and reliability. At the core of these standards lies cleanability—the capacity of a device or component to be effectively cleaned, sterilized, and maintained without compromising its integrity or functionality. Custom silicone parts have emerged as a pivotal element in achieving superior cleanability, owing to their unique material properties and design flexibility.
In this comprehensive exploration, we delve into how innovative design strategies for custom silicone components optimize cleanability, ensuring patient safety, regulatory compliance, and long-term durability of medical devices.
Understanding the Importance of Cleanability in Medical Devices
Regulatory Standards and Industry Requirements
Healthcare regulators worldwide, including the FDA, ISO 13485, and European MDR, emphasize cleanability as a fundamental criterion in medical device approval. Devices that are difficult to clean pose a risk of biofilm formation, cross-contamination, and infection transmission. Therefore, designing components that facilitate easy, thorough cleaning is not just best practice but a regulatory imperative.
Risks of Poor Cleanability
- Biofilm Accumulation: Microorganisms can adhere to complex surfaces, forming resilient biofilms that resist sterilization.
- Cross-Contamination: Inadequately cleaned parts can harbor pathogens, risking patient safety.
- Device Failure: Residual contaminants may degrade material properties over time, leading to malfunction.
- Regulatory Non-Compliance: Non-conformance to standards can result in product recalls and legal liabilities.
Why Custom Silicone Parts Are Ideal for Medical Device Cleanability
Unique Material Properties of Silicone
- Non-porous Surface: Silicone's smooth, non-porous surface resists microbial adherence and allows for easy cleaning.
- Chemical Resistance: It withstands a broad spectrum of cleaning agents and sterilization methods (autoclaving, ethylene oxide, gamma irradiation).
- Thermal Stability: Maintains integrity under high temperatures, facilitating effective sterilization cycles.
- Biocompatibility: Silicone is inert, hypoallergenic, and safe for direct contact with tissues and bodily fluids.
Design Flexibility and Customization
- Complex Geometries: Silicone can be molded into intricate shapes, enabling design features that minimize crevices and dead zones.
- Integrated Features: Incorporation of channels, valves, or slots in a single piece reduces assembly points where dirt or microbes can accumulate.
- Surface Finish Control: Custom surface texturing or polishing can be tailored to optimize cleanability without compromising function.
Design Strategies for Enhancing Cleanability of Custom Silicone Parts
1. Simplify Geometries to Minimize Crevices and Dead Zones
Complex geometries with sharp corners, internal cavities, or hidden recesses pose cleaning challenges. Designing smooth, streamlined surfaces with gentle curves and minimal internal angles ensures accessible cleaning and sterilization.
2. Optimize Surface Finish for Maximum Hygienic Compatibility
Achieving a high-quality surface finish—preferably Ra (roughness average) below 0.8 micrometers—reduces microbial adhesion. Polished or textured surfaces should be carefully selected to balance ease of cleaning with functional requirements.
3. Incorporate Self-Draining Features
Designing self-draining geometries prevents fluid pooling, which can harbor microbes. Including drain holes or sloped surfaces ensures residual liquids are efficiently removed during cleaning processes.
4. Use of Surface Coatings and Treatments
Applying antimicrobial coatings or low-friction, non-stick surface treatments can further enhance cleanability. These coatings inhibit microbial growth and facilitate easier removal of biofilms during cleaning cycles.
5. Design for Compatibility with Cleaning and Sterilization Protocols
Ensure all silicone parts are compatible with standard sterilization methods—such as steam autoclaving, ethylene oxide, gamma irradiation, or chemical disinfectants—without degradation. Material selection should be aligned with the intended sterilization process.
Manufacturing Considerations for High-Quality Custom Silicone Parts
Injection Molding Precision
Advanced injection molding techniques enable tight tolerances and surface finishes required for optimal cleanability. Cleanroom manufacturing environments prevent contamination during production.
Material Selection and Validation
Choosing medical-grade, USP Class VI silicone ensures compliance and safety. Material validation involves rigorous testing for leachables, extractables, and biocompatibility.
Quality Control and Inspection
Implementing non-destructive testing methods such as CMM (Coordinate Measuring Machines) and surface roughness testing guarantees that parts meet design specifications for cleanliness and function.
Case Studies: Successful Integration of Custom Silicone Parts for Cleanability
Case Study 1: Silicone Seals in Sterile Fluid Delivery Systems
By designing integrated, smooth-surfaced silicone seals with self-draining features, manufacturers achieved significantly reduced cleaning times and improved sterilization efficacy. The elimination of complex joints minimized microbial harborage points.
Case Study 2: Silicone Catheter Components with Enhanced Surface Finish
Implementing high-polish silicone components with optimized geometries led to lower biofilm formation rates and extended device lifespan, ensuring safer patient outcomes.
Future Trends in Custom Silicone Design for Medical Cleanability
- Smart Surface Technologies: Development of antimicrobial silicone surfaces that actively inhibit microbial growth.
- Additive Manufacturing: Exploring 3D printing of silicone for rapid prototyping and complex geometries that enhance cleanability.
- Integrated Sensor Systems: Embedding sensors within silicone components to monitor cleaning efficacy and sterilization cycles in real time.
Conclusion: Achieving Excellence in Medical Device Hygiene Through Thoughtful Silicone Design
The integration of custom silicone parts in medical devices offers unmatched opportunities to enhance cleanability, ensure patient safety, and meet regulatory standards. By adopting strategic design principles—including simplified geometries, surface optimization, and material validation—manufacturers can produce high-performance, hygienic, and durable components.
Investing in innovative design and manufacturing processes for silicone parts not only elevates device hygiene but also fortifies trust with healthcare providers and patients. As the industry advances, the emphasis on cleanability-driven design will continue to be a cornerstone of medical device innovation.
Table 1: Key Design Features for Cleanable Silicone Parts
Feature | Description | Benefit |
---|---|---|
Smooth, Rounded Surfaces | Minimize crevices and sharp angles | Reduce microbial harborage |
Self-Draining Geometries | Sloped surfaces and drain holes | Prevent fluid pooling |
High-Quality Surface Finish | Ra < 0.8 micrometers | Facilitate cleaning and sterilization |
Integrated Features | Fewer joints and seams | Minimize contamination points |
Surface Coatings | Antimicrobial and non-stick layers | Inhibit microbial growth |
By embracing these design principles, we can ensure that custom silicone parts in medical devices not only meet but exceed industry standards for cleanability, ultimately safeguarding patient health and enhancing device longevity.